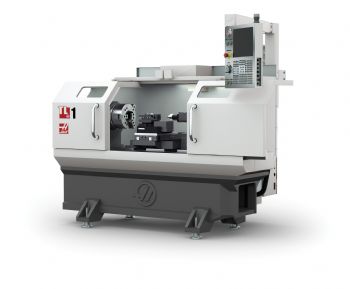
The range of tool-room lathes from Haas Automation, Norwich (
www.haas.co.uk) has been designed to be affordable and easy to use, while offering the precision and control of the Haas CNC system; and with the Haas Intuitive Programming System, manual machinists will find the move to full CNC both quick and easy — and will be cutting parts in minutes.
The TL-1 lathe recently underwent a complete redesign; it now features a new enclosure and higher overall performance. It has a maximum machining capacity of 406 x 762mm, a 508mm swing over the front apron and an A2-6 spindle nose that accepts either an 8in or 10in three-jaw manual chuck.
The updated TL spindle, which has a 3in bore, is powered by a 12hp vector drive system. As standard, it has a maximum speed of 2,000rev/min (optionally 3,000rev/min), and the rapid-traverse rate for both the X and Y axes has increased to 11.4m/min.
A manual tailstock is available as an option for additional part support; and to better contain swarf and coolant — and protect the operator — a full metal enclosure is now standard.
The TL-1 comes equipped with Haas Automation’s Intuitive Programming System, a proprietary conversational operating system designed to make programming particularly straightforward; an interactive graphical interface guides the operator through the steps necessary to machine a part.
Furthermore, operations that would be difficult or even impossible on a manual machine — such as compound angles, radii, tapers, profiles, ID and OD threading and rigid tapping — can be undertaken with no knowledge of G-code programming.