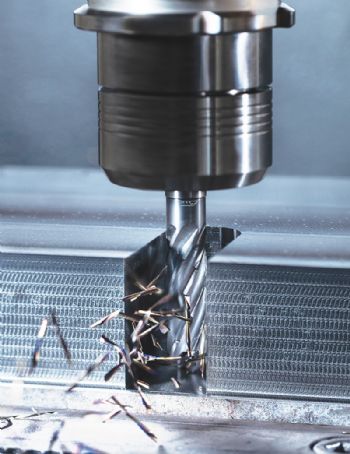
Over the last five decades, the demands placed on the machining industry have changed considerably: components are becoming ever more complex; and companies are under immense pressure to minimise lead times and costs.
To remain competitive, it is becoming increasingly important for companies to fully exploit advances in machining, such as trochoidal milling — a method of machining with an end mill using a circular movement, light cuts and the full length of the cutter flutes.
The combination of new CAM programming systems and appropriately developed tooling means this machining strategy offers increased process reliability, along with significant savings in time and cost.
The benefits of trochoidal milling are particularly noticeable when machining high volumes, deep slots or high flanks. In addition to extremely high process reliability and considerable time savings, reduced tool wear is achieved.
This is because during trochoidal milling the angle of engagement remains as small as possible; this reduces vibration and gives the end mill more time to cool down during the machining process.
The new CircularLine CCR end mills from Sheffield-based WNT (UK) Ltd (
www.wnt.com) have been designed to achieve optimum results when using the trochoidal milling process.
These tools feature WNT’s Dragonskin coating; they are also extremely robust and wear-resistant and can withstand significant temperature fluctuations. Furthermore, these end mills feature a special chip breaker that is ground into the cutting edge geometry.
The need for this becomes apparent when considering that chips produced by a 12mm-diameter tool with a cutting length of 4xD and no chip breaker would be 48mm long. The chip breaker restricts the chip length to 2xD, ensuring optimum chip removal — even when machining ‘problematic’ materials.
WNT offers two versions of these end mills: one for universal applications and another specifically for machining aluminium. The six-fluted CCR-UNI ensures smooth operation and a high material removal rate at cutting depths
up to 3xD (steel), while the four-fluted CCR-AL accommodates cutting depths of 4xD (aluminium).
Tests have shown, it is possible to use significantly higher cutting data when using trochoidal milling with CCR end mills than with conventional machining processes, shortening machining times considerably. Even applications that were previously considered to be very difficult have been dramatically improved.
In the past, problems regarding chip evacuation were invariable encountered when machining stainless steel 1.4404 (Duplex-VA). Unusually for this material, it was machined without coolant during tests.
Moreover, these tests showed that, compared with wet machining, the thermal shock effect was minimised and considerably longer tool life could be achieved. In one case, the conventional machining time for a workpiece was reduced from 12min to 5.5min — and the tool life tripled.
The gains that can be made using CircularLine CCR end mills and the trochoidal machining process can be seen in the featured video on Machinery Market’s homepage (
www.machinery-market.co.uk).