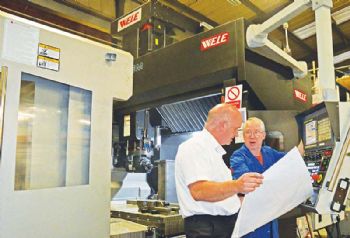
By installing a Wele bridge-type vertical machining centre, Glassworks Hounsell (GWH) now has an effective five-face processing capability that has allowed it to combine six or seven operations into just two.
Furthermore, the company is now expanding its sub-contract production services into new areas and attracting new customers.
Sales director William Brinkman said: “The additional capacity of the Wele SB316M is opening new doors for us; its high levels of rigidity, flexibility and accuracy are transforming our ability to produce larger components. The machine has not only given us the opportunity to expand the range of services we offerto existing customers but also attracted new customers wanting local UK supply.”
GWH, which is based in Halesowen, has built group sales up to over £6.5 million through its supply of specialist equipment for feeding raw material into glass furnaces used by the international glass industry.

Over the last 30 years, the company has supplied some 1,200 ‘feeders’, 95% of which have been exported to more than 50 countries. It also produces the tin oxide electrodes and ‘connector systems’ that allow glass furnaces to operate at temperatures between 870 and 1,650°C.
In addition, GWH manufactures polished-steel marver tables (used for shaping glass), plus hand-held ‘blowing irons’ (used to blow the glass into the required shape).
The company also builds and reconditions GN Flexo narrow-web flexographic four-colour printing machinery, as used by companies in the packaging industry — particularly those involved in confectionery.
Jeff Blackborow, GWH’s operations manager, said: “Having developed products that require a lot of technical input, we are now seeing an increasing demand for larger units — especially from overseas customers. This demand meant that we needed to upgrade our in-house machining capability.”
As a result, GWH researched the market for bridge-type machining centres. It compared ‘value and return generated against cost’, along with the ability of suppliers to provide the required levels of service and support, and finally selected the Wele machine from Hinckley-based 2D CNC Machinery Ltd (
www.2DCNC.co.uk).
The heritage and track record of Wele were also important factors in the decision-making process: Wele is part of the JTEKT Group, itself a sub-group of Japanese car maker Toyota and owner of international machine tool builders Mitsui Seiki and Toyoda.
Sub-contract work
GHW previously sub-contracted its larger components, but with an expanding product range, the company decided it needed to protect its core competences, which include AutoCAD and 3-D modelling, as well as turning, milling and fabricating using MIG, MMA and TIG to weld mild steel, stainless steels and aluminium.
Recently completed in the fabrication bay was a 3m-high x 13m-long boom feeder for a glass furnace in Spain. The company also has a specialist painting facility, which gives it a ‘one-stop’ capability.
The Wele SB316M has a 3,000 x 1,500mm table, a work envelope of 3,060 x 1,600 x 800mm and a 1,700mm gap between its two columns.
Accuracy over the full extent of the axis travels is ±0.01mm, and the repeatability is ±0.003mm. The 26kW BT 50 gear-driven spindle (740Nm of torque) has a speed range of 10-6,000rev/min and a through-tool coolant feed. There is also a 32-tool magazine. In preparation for the installation, GWH laid a 1.2m-deep concrete foundation in the shopfloor.
Mr Blackborow said: “We are serious in our machining capability, so the floor was important. We did not want to limit the amount of material we could remove, nor compromise the tolerances we can maintain — or the geometric relationships we achieve when using the five-face capability.”
He says the Wele machine replaced a horizontal borer that needed a highly skilled operator to use it and was uneconomic on small batches — particularly when the parts were complex.
GWH now has sub-contract business opportunities in the offshore, power generation, nuclear, marine and aerospace sectors, which makes the Wele a particularly important installation.
The machine is currently run single shift by a recently taken on setter operator who takes GWH’s head count to 27; and since being installed last March, the largest batch has been five components.
Some 40% of the Wele’s production has focused on in-house work, such as the massive machine frames for the material feeders.
Growth in sub-contract work has included the production of some difficult injection mould tooling, which Mr Blackborow says would not have been viable without the Wele machine.
To date, programming has been carried out at the Fanuc 18iM control, but off-line programming will be introduced in the near future.
With production on the Wele now settled, GWH is reorganising its machine shop and disposing of redundant equipment; the company has also installed a biomass heating system and new measuring facilities.