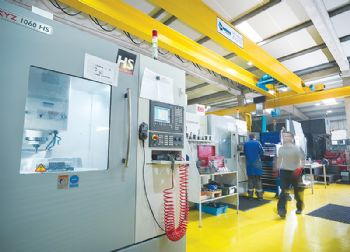
The beginning of Investment Casting Systems (ICS) is a fairly familiar story, with founder Ted Head turning his mechanical-engineering design and manufacturing expertise — along with professional model-making skills — into the successful engineering business that it is today.
Starting out in his garage with a bench lathe and a small milling machine some 37 years ago, Mr Head turned his hand to general sub-contract engineering before quickly moving into tool making and growing the business into an eight-man operation during the 1980s.
Success at tool making provided the opportunity for ICS to diversify when a customer asked if the company could also provide an injection moulding service; this grew rapidly to account for about two thirds of the company’s turnover, with the processing of over 800 tonnes of raw material annually.
As a result, tool making became a support service for this side of the business, with tool maintenance and the build of new tools for its in-house requirements. ICS also continued to invest to ensure that it achieved ISO 9001:2008, AS 9100 Rev. C and World Class Tool Maker accreditations. The company has also been awarded the SC21 Bronze award.
Over the past four years, ICS has spent more than £600,000 on machine tools and infrastructure, allowing it to re-enter the sub-contract tool-making sector and produce close-tolerance tooling for a variety of industries, including power generation and aerospace (this recently resulted in a £750,000 export order to the USA for carbon composite products, an area that ICS is expanding into).
A helping hand
ICS technical director James Head says helping the company’s development are a number of machines from XYZ Machine Tools (
www.xyzmachinetools.com).
“We bought our first XYZ machines — a Pro 2000 turret mill and a DPM bed mill — 15 years ago, and they are still with us today. Since then, we have continued to invest in XYZ machines because they provide exceptional quality at a good price, they are accurate and stand up to the test of time.”

Their accuracy and longevity were highlighted during a recent assessment of all the machines in the tool-room as part of ICS’s World Class Toolroom/ISO 9001 status.
“To maintain our world-class status, we have to have our machine tools laser calibrated to within 5µm/m, so we are confident that we can repeat processes on any machine. All of the XYZ machines came within that, even our seven-year-old XYZ 1060HS.”
Of the 12 XYZ machines at ICS, four are XYZ 1060 HS vertical machining centres. These high-speed machines feature a 12,000rev/min 20hp spindle, 43m/min rapid-traverse rates, and a temperature-controlled spindle and ballscrews for enhanced accuracy. Control is provided by a Siemens 840D high-speed ShopMill control.
Mr Head says: “When we first looked at the XYZ machines, the Siemens control was an issue, because other controls tend to be the norm in the world of tool making, but all of our tool makers have taken to it, with ease of use being
a major advantage. The control also comes with features that are considered extras with other machine suppliers.”
The confidence that ICS has in the XYZ machines means that they are also used ‘lights out’ at the weekend. Some of the larger mould tools have single program cycle times of 75hr, so the company schedules these jobs for Friday afternoon and leaves them running over the weekend.
“This ability to run ‘lights out’ effectively gives us free machining time on a lot of jobs, leaving the machines free during the manned hours to fit in shorter-cycle more-urgent work.”
Machining composites
The latest XYZ Machine to be bought by ICS is an XYZ 710 vertical machining centre, because the lack of space precluded a fifth XYZ 1060 HS.
With the development of a new composites division — Technical Composites Systems (TCS) — floor space in the tool-room was restricted, but the 710 x 450 x 500mm work envelope of the XYZ 710 will provide the additional machining capacity that will be used as the new company develops.

TCS director Mike Sloan says: “We created the company in 2016 to address what we saw as opportunities in the world of composite manufacturing.
What we have created is a comprehensive manufacturing facility for the aerospace and defence sectors. It has been structured to maximise the synergy between our tool-room activities and the world of composites.”
With extensive experience of manufacturing tooling for the composite industry, this new division will further enhance the services provided by ICS by adding design services, tooling, material selection, manufacturing and finishing of a range of materials, including carbon fibre, Kevlar and glass fibre.
While the initial focus will be on providing services to external customers, there are plans to develop OEM composite components in the longer term.
“Most of the tooling we make for the composite industry is going to aircraft seat manufacturers — mainly for making first-class and super-first-class seats.
“These are manufactured from composites to save weight — and an enormous amount of fuel every year.”