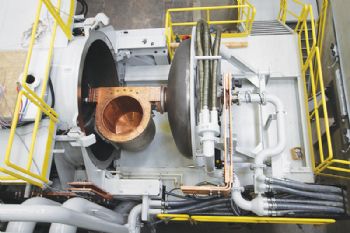
A castings facility capable of producing some of the biggest titanium aerospace components in the world is now operational at the University of Sheffield Advanced Manufacturing Research Centre (AMRC) (
www.amrc.co.uk).
Construction of the furnace for the AMRC Castings Group was completed last year, and the first ‘hot commissioning’ tests have been completed successfully in the past few weeks.
The furnace has three interchangeable crucibles with the capacity for melting 250kg, 500kg and 1,000kg of metal respectively. A molten mass in excess of 1,000kg is required to make a 500kg titanium casting, and only a handful of furnaces exist globally that are capable of casting near-net-shape aerospace components of this size.
With leading aerospace companies already lining up to collaborate on research, AMRC Castings is conducting studies to identify the risks associated with casting large-scale near-net-shape components in titanium.
The aim is to refine and enhance the casting process to ensure that casting can create lower ‘buy to fly’ ratios (the weight ratio between the raw material used for a component and the weight of the component itself) for large-scale aerospace components, while maintaining performance that is comparable to their forged counterparts.
Mark D’Souza-Mathew, AMRC Castings research and development manager, said: “The cost savings with near-net-shape castings are huge, with efficiencies relating to wastage and time-savings on the machining and finishing processes. Buy-to-fly ratios are improved from 5:1 with typical forged components down to 1.5:1 via the cast route.”
He says that casting can produce superior material properties to those offered by both forged and machined components, adding that the new furnace built at AMRC Castings’ facility features enhanced cooling to better control the material micro-structure.