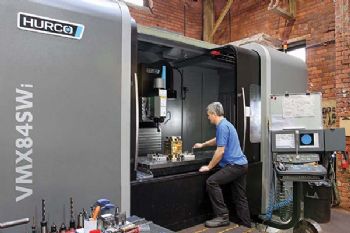
For the latter half of its 16-year existence, the sub-contract machining firm Ian Cocker Engineering has relied almost exclusively on vertical machining centres from one supplier to produce prismatic components, mainly for the oil and gas sector — frequently from difficult-to-machine materials such as stainless steel and Inconel.
To extend its capacity in terms of both size and versatility, the company recently installed its first five-axis machine — a Hurco VMX84SWi from High Wycombe-based Hurco Europe Ltd (
www.hurco.co.uk). This machine — the largest in the manufacturer’s VMX range — was the first of its type to be installed in the UK.
Proprietor Ian Cocker said: “The large working envelope means that we can machine parts that we previously had to turn away; and we produce them cost-effectively because the machine has an integral B-axis spindle head — plus we have added a fifth CNC axis by purchasing a Kitagawa rotary table.
“It is a very versatile five-axis solution. We can use the rotary table either upright or on its back to tackle five sides of a component in one hit. We can also use it for fully simultaneous five-axis cycles; and if we take the Nikken unit off the table, components over 2.1m long can undergo CNC milling and drilling cycles using up to four axes.”
In 2014, high-volume production for the oil and gas industry accounted for 80% of Ian Cocker’s turnover, but this halved when the slowdown in the sector took hold.
Fortunately, much of the shortfall was replaced by development contracts in the same field, while additional work was won from the AMRC at Sheffield University and from Sheffield Forgemasters.
A batch of components for the latter customer was one of the first jobs to be put on the VMX 84SWi. The project involved re-engineering seven 1m-long rack segments for the axis drives of a Chinese-built floor-type milling machine in use at Sheffield Forgemasters. Each segment required 40 teeth to be machined at an 11deg angle to an accuracy of ±15µm.
Mr Cocker says: “Having the B axis on the big machining centre was ideal for completing this job, as it avoided having to tilt the components to mill the teeth and chamfer the end of each tooth.”
Time savings
Another job recently completed on the machine involved 3+2-axis milling of a test equipment component requiring angled ends and slots.
Previously, it took a couple of hours to set up the job on a three-axis machine, because the part had to be tilted and test cuts made and measured before production could start. Setting the same job up on the Hurco five-axis machining centre — using Renishaw part-probing — takes about 10min, saving an enormous amount of time.
Mr Cocker says sub-contractors have a tendency to take on work that is right on the physical limits of their capacity — or even a little too big — then improvise to get round the problem by re-fixturing the component and taking off end guarding — or whatever is deemed necessary.
For Ian Cocker, this approach is in the past, as the 2,135 x 865 x 760mm work envelope of the VMX84SWi is more than sufficient to accommodate all jobs coming from the sub-contractor’s current customer base. Indeed, this machine has differentiated the company from its competitors, allowing it to take on niche work that others cannot tackle.
Moreover, this advantage is about to be taken a step further, as Mr Cocker recently upgraded the CAM system that the company used for off-line G-code programming to a seat of Open Mind’s HyperMill five-axis CAM software.
This provides the ability to produce fully interpolative five-axis cutting cycles to run on the new Hurco machine, allowing Mr Cocker to undertake work requiring complex features and profiling.
That said, 19 out of every 20 cutting cycles for the company’s four Hurco machining centres — including 3+1 routines, as well as 3+2 ones for the new machine — are prepared using WinMax 9 conversational programming software running in the machines’ proprietary control systems.
Mr Cocker says: “WinMax programming software is incredibly easy to use. It was a big factor in our purchase in 2008 of our first Hurco machining centre — a VMX 50 that can be up and running in five or 10min to produce a new job.
“At the time, we benchmarked the machine against a model with a conventional control from another supplier. After speaking with users of both types, we concluded that by the time we were cutting on the Hurco, we would still have been programming the other machine.”