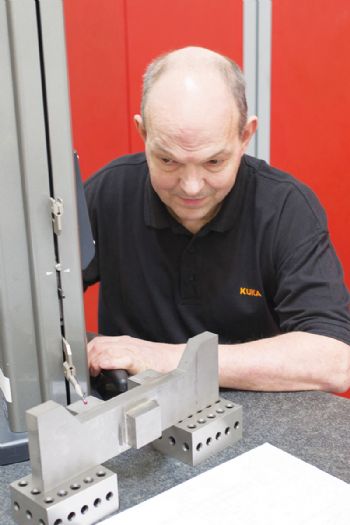
The largest-ever research project backed by Innovate UK for developing cost-effective titanium-alloy structural airframe parts is nearing completion.
The three-year £2.6 million TiFab programme has studied more than 170 aircraft components to assess their suitability for an advanced joining process that could offer annual raw-material savings of around £9 million.
TiFab consortium members — CAV Advanced Technologies, KUKA, Ten Solutions, Thompson and TWI — predict that manufacturers could save over 200 tonnes of titanium a year if they chose linear friction welding (LFW) to bond parts instead of machining from solid billets.
The project has been designed to show how near-net-shape manufacture can boost productivity by using tailored blanks to produce lightweight titanium alloy parts, the main aim being to develop an industrial-scale demonstrator tooling system and components.
Project leader Martin Wood, from CAV Advanced Technologies, said: “LFW was preferred to other welding or deposition techniques because of its speed and its ability to achieve ‘near parent’ material properties.
Currently, forgings and extrusions are the only tailored-blank solutions suited to primary airframe-structure components, because material physical properties must be used to the maximum in order to minimise weight.”
With the support of several OEMs, the project team has been able to examine a vast number of ‘candidate’ parts, create design solutions for tailored blanks and establish weld-process parameters.
“We’ve accomplished a 100% success rate in producing tailored-blank solutions, which also delivered at least 30% in material savings. It’s a remarkable achievement, especially as we didn't know what parts would be supplied by the OEMs.”

The suitability of LFW for the manufacture of titanium aerostructure parts has been evaluated by welding experimental ‘coupons’, thereby allowing the team to establish the conditions that produce good-quality welds in terms of metallurgical and tensile performance for 25mm-thick Ti-6Al-4V grade 5 material (specification AMS4911).
High-quality welds were made in an unprotected atmosphere, at all the pressures applied (down to 5MPa) when a high average rubbing velocity of 500mm/sec was used. Weld times varied from 0.7 to 6.3sec, depending on the friction pressure applied.
All the ‘weldments’ produced exhibited a characteristic fine-grained equi-axed microstructure, free from voids, surface contaminants and α-case ingress within the weld line. At an average velocity of 400mm/sec, pressures between 80MPa and 150MPa were found to be most effective.