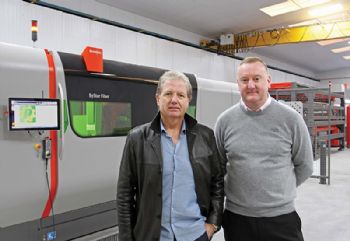
Ian Hazlehurst (pictured right), who established the sub-contracting firm Machfab Engineering in 2004, has an extensive background in traditional precision engineering.
He recently joined forces with business entrepreneur Russ Canner, after they identified a gap in the local market for a firm capable of providing a comprehensive range of services that include sheet-metal cutting, bending and fabrication — plus powder coating.
With the assistance of a regional growth fund grant, Proform has invested over £2.5 million in premises and some of the highest-specification machinery available. The company says it will create 28 jobs in its first year of business and hopes to continue to expand on this year on year.
A turnover of £1.2 million is expected in the first year of trading, and the directors hope to double that by the end of the fifth year. These figures are based on Proform’s current capacity, which comprises a fibre laser cutting machine, two press brakes and a twin-head 3-D water-jet cutting machine — all supplied by Coventry-based Bystronic UK Ltd (
www.bystronic.com).
The equipment is installed in a 22,000ft
2 facility in Prenton (a suburb of Birkenhead). The sub-contractor has also installed MIG and TIG welding bays and bought a nitrogen-generating plant to supply the current fibre laser machine and another in the future.
This cutting gas provides a high-quality cut edge; oxygen will be used only on sheet over 6mm thick and when cutting copper. By the middle of this year, a powder coating plant will be installed to augment the wet-spray-painting service offered, bringing the total investment in the venture to £3.3 million.
Preliminary investigation
Highlighting the background to this new venture, Mr Hazlehurst said: “We polled over 30 of Machfab’s customers and found that they were spending £1.5 million on buying in laser cutting services, so we reasoned that we could win a proportion of that.
Another consideration was that there are just two sheet-metal sub-contractors in the Liverpool area and they cannot provide the full range of machining services. The next nearest providers are in Manchester and North Wales.
“It was also apparent that the general standard of service provided could be improved upon. Through experience at Machfab of buying in laser cutting services, we noticed that quality was sometimes suspect and turn-round times were often much longer than promised.

“These were the factors that prompted myself and Mr Vanner to set up Proform. It is our intention to be a serious contender and take the sub-contract sheet metal-working market in the North West by storm.”
“An important facet of the company is that it offers an ‘all-encompassing’ design and manufacturing service, which is why it bought laser cutting, water-jet cutting and folding equipment from the outset; and Proform opted to buy from Bystronic, because it was the only manufacturer able to supply all three types of machine.
“They are built in Switzerland, at the company’s factory in Niederönz, and they all use the same production planning and control software — BySoft 7. This means that programs can be generated from a CAD model to drive the three different types of Bystronic machine, so components can be transferred easily from one to another with little production down-time.
“The ByJet Flex has two CNC heads and a 6 x 3m bed, making it the only machine of its type and size in the North of England (all other Bystronic machines of this size and specification are in the South). Any material up
to 300mm thick can be cut to very high accuracy.
The ByStar Fiber laser cutting centre also has a 4 x 2m capacity rather than the normal 3 x 1.5m; it was the first machine of this size to be delivered by Bystronic in the UK. Its 6kW fibre laser source can cut 25mm-thick mild steel, 30mm stainless steel and aluminium, as well as 15mm copper and 12mm brass.
Automated handling
The machine has been equipped with a ByTrans sheet-handling system capable of delivering material automatically to the shuttle table and subsequently retrieving the processed sheet.
Apart from eliminating arduous manual sheet handling, this has the potential to boost output considerably; it can be stocked with up to six tonnes of material to allow unattended production overnight.

Press braking is undertaken by an Xpert 250-tonne machine (capable of bending components up to 4.1m long) and an Xpert 40; this is Bystronic’s smallest model,with a 40 tonne/1m capacity.
About half of the output from the laser cutting centre is folded on these two machines. Mr Hazlehurst says that an integral feature of the larger CNC press brake is the large depth of the back-gauge, which maximises the range of parts that can be produced.
He also appreciates the LED lights along the upper beam; these show where the bending tools should be placed for any particular job. There are also cameras either side of the machine to verify that the correct punch and die have been selected. The result of these safety measures is that damage to tooling is avoided, and scrap is eliminated.
Regarding the Xpert 40, Mr Hazlehurst highlights its user-friendliness and sheer speed when bending parts up to 1m long.
The 25mm/sec stroke is 2.5-times faster than on the Xpert 250, the tooling is interchangeable, and power consumption is low — as it is on the fibre laser, which draws about a third of the electricity consumed by a CO
2 laser.
Mr Hazlehurst anticipates that the fibre machine will generate two thirds of the company’s turnover, being up to three-times faster than a CO
2 equivalent, especially on thinner gauges. It can also cut a wider range of materials without the risk of damage to the optics.