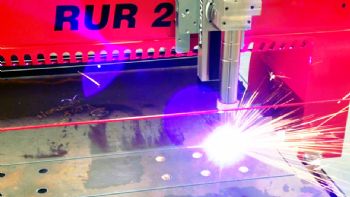
Established 70 years ago in a blacksmith’s shop, the family-run business John Thorburn & Sons Ltd now works from a 1.5-acre site in Duns (in the Scottish borders), serving the construction, agriculture and commercial steel-working sectors.
The company employs more than 50 people, who operate a variety of metal-working and fabricating equipment for the manufacture of agricultural buildings and structures (
www.jthorburn.co.uk).
John Thorburn & Sons used to rely on its steel-working and fabricating equipment until it bought an RUR2500 plasma cutting machine from Rochdale-based Kerf Developments Ltd (
www.kerfdevelopments.com).

Managing director John Thorburn said: “We recognised that our method of cropping, punching and drilling plates was cumbersome, time consuming and slowing down our throughput. All our jobs had to be handled and reworked on a variety of different machines to arrive at a finished part.
“Additionally, we had to stock a large range of steel bar widths and thicknesses, and this was taking a lot of floor space. The Kerf machine instantly eliminated all of these issues.
“We specified the RUR2500 with a 6 x 2m bed, so we could comfortably fit 4 x 2m x 20mm-thick plate on the machine and use its nesting facility to cut up to 50 stanchion base plates in a single set-up.”
These base plates were previously cut from 6,400mm-long bar that was 400mm wide x 20mm thick. According to Mr Thorburn, the change from bar to plate has taken stanchion material costs from £15 to less than £10 per unit.
“While the material savings have been significant, we bought the machine to streamline productivity, and it has certainly done that.
“Stanchion plates used to require manual cropping, punching and drilling, which was a full-time job for our staff. The production time used to be almost 20min per plate; the Kerf plasma has reduced this to less than 2min.
“Moreover, once the plasma machine has been set up, our staff can carry on with welding jobs.”