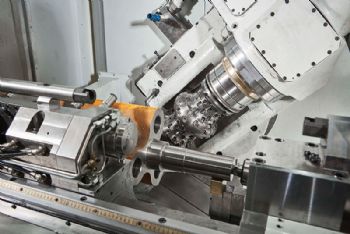
Holroyd (
www.holroyd.com), the Rochdale-based Precision Technologies Group company, has developed a new CNC profile-milling machine that — in addition to producing helical rotors — can be programmed to produce straight-fluted components as used in Roots-type blower ‘air ends’.
Although it is part of the company’s EX range of rotor-milling machines, the new 4EX-R-BL has been designed ‘from the ground up’.
As well as being equipped to mill helical rotors up to 450mm in diameter, the 4EX-R-BL can rough-mill blower blanks up to 320mm in diameter and 900mm long into straight-fluted rotors in a floor-to-floor time of 30min, ready for profile milling to final size.
This represents a significant time saving when compared with the 1.5-2hr typically required to cut individual Roots-type blower rotor flutes, using traditional milling techniques.
Until now, manufacturers producing rotors for Roots-type blowers have been forced to rely on either CNC flat-bed milling machines or machining centres adapted to absorb the vibrations that occur during flute milling.
When using either of these methods, each flute has to be milled in a separate operation; as a result, the machining process for Roots-type rotors has always been labour-intensive and costly, says Holroyd.
By contrast, the technology offered by the 4EX-R-BL moves manufacturing away from traditional flat-bed milling, where the component would be manually turned after producing each flute, to a programmable and fully automated process that can machine both two- and three-flute blowers in one sequence.
To remove the need for manual intervention or indexing during the milling of each flute, the Holroyd machine features a bespoke steadying system that has been designed to withstand the additional forces generated during the milling of straight flutes.
Specially developed ‘finger clamps’ ensure that the workpiece is held securely when a flute is being milled. These then release to allow automatic rotation and positioning, ready for milling the next flute.
The maximum component weight that can be accommodated by the 4EX-R-BL is 900kg, while the maximum work traverse is 1,600mm. The cutter head can accommodate tungsten carbide and HSS tooling systems using an HSK160 interface.
The cutter speed (steplessly variable, unidirectional) is 20-250rev/min, while the maximum spindle torque (at 105rev/min) is 600Nm. The maximum head angle is +90/-55deg, and control is via a Fanuc 31i.