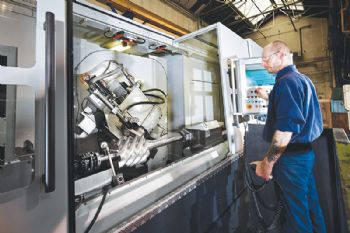
Rochdale-based Holroyd Precision, a manufacturer of high-precision grinding machines, has sold a TG 350 rotor-grinding machine to a leading Japanese manufacturer of rotors for refrigeration compressors.
The machine will be installed in August in the compressor manufacturer’s Hiroshima facility, where it will be used to precision-grind cast-iron and stainless-steel screw rotors up to 350mm in diameter, for use in industrial refrigeration units (
www.holroyd.com).
Mark Curran, Holroyd Precision sales manager, said: “A long-standing customer, with nine of our machines in daily use, the Japanese company has traditionally rough-milled and then finish-milled helical rotors, prior to ‘final’ precision cutting.
“The finished profile shape is machined onto the cutter using a Holroyd CS 500 tool management centre. With a wide range of rotor types to manufacture, however, it became apparent that making the switch to CNC grinding would be beneficial.”
The TG 350 rotor-grinding machine will give the refrigeration specialist higher levels of accuracy, speed and repeatability — primarily as a result of greater levels of automation and reduced set-up times.
For instance, where it can presently take the company up to 50min to manufacture rotors up to 120mm in diameter by ‘milling and cutting’, Holroyd has been able to demonstrate a time saving of around 35min.
A key factor is that, on Holroyd TG-series machines, diamond dressing wheels continuously dress during the cycle.