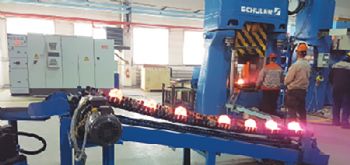
The Chinese automotive supplier Chongqing Lianhao Technology has ordered four mechanical forging lines from the German press manufacturer Schuler (
www.schulergroup.com) .
The multi-station mechanical presses feature a link drive and have a press force of between 8,000 and 20,000kN. The manufacture and assembly of the four forging lines will take place at Schuler’s Göppingen and Erfurt sites, with delivery planned to take place in the first half of 2018.
With a stroke range of 250-800mm, these type MML2 presses are suitable for the mass production of a wide variety and size of drivetrain and chassis components — from bevel gears to transmission shafts.
The link kinematics reduce the forming speed, thereby increasing both the quality of the parts and the formability of the material.
In another recent forging application, Schuler installed two automated lines at Darkhan Metallurgical Plant in Mongolia (pictured), each comprising induction heaters, short-stroke die forging hammers and a robot. These will be used to produce steel balls in the diameter range 100-140mm.
In the first step of the process, round steel bar is cut into appropriate lengths by a circular saw and heated by induction. Next, a robot arm takes the red-hot parts from the conveyor belt and inserts them into the press.
The forged steel balls are then removed by an employee from a discharge chute integrated into the die area.
After quenching, hardening, tempering and inspection, they are ready for use — ‘grinding’ mineral ores, of which there are vast deposits in the country.
Each line produces a new steel ball every 8sec, and the annual capacity of both lines is 25,000 tonnes.