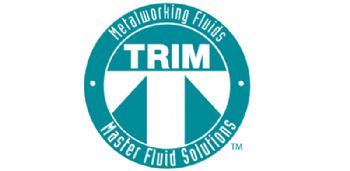
For the German CNC machining company K&P Frästechnik, investment in new machinery to meet increased demand for its prototyping and short-run machining work did not achieve the early success the company had planned.
The type of metal-working fluid it had been using for years was unable to maintain production quality when faced with the higher machining speeds and coolant pressures of the new machines; the emulsion being used split into oil and water.
The old coolant was pumped out and the machines were filled with an alternative, but that too started to fail within a matter of weeks.
A huge quantity of scum was produced, and this attacked aluminium components, causing black marks to appear on the material.
After further draining, cleaning and refilling, additional biocides were added to the coolant with the aim of preventing fungal attack. However, all efforts proved futile, and the problems remained.
In a last-ditch attempt to resolve the situation, K&P Frästechnik contacted the Frankfurt-based metal-working supplies company Graushaar, which recommended Master Fluid Solutions Trim MicroSol 519 (
www.masterfluidsolutions.com); the trial of this fluid proved to be a turning point.
Unlike all the other coolants that had been tried, this one remained biostable without the need for any additives; it also kept the machines clean and — most importantly — assured the quality of the end product.
K&P Frästechnik co-owner Ralf Kusch said: “Our machines have been running absolutely perfectly for two years now, using the Master Fluid Solutions metal-working fluid. Through long maintenance intervals alone, we are saving several thousand euros a year.”
The Trim range from Master Fluid Solutions is developed in the company’s UK laboratories in Needham Market. Trim MicroSol 519 is a general-purpose metal-working fluid that is both boron- and formaldehyde-free; it provides medium to high levels of lubrication without the need for chlorinated or sulphurised extreme-pressure additives.
Moreover, very little of the fluid is lost on workpieces and swarf; and when topping up the fluid, a 1% solution is sufficient, where 2-4% was previously required.