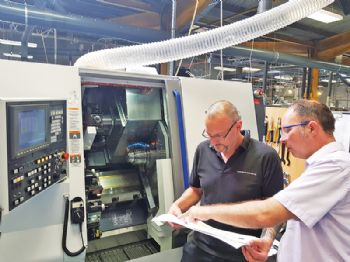
Some 1.5 million components a year are despatched from the Worthing-based precision sub-contract machinist Roscomac, which is achieving record on-time deliveries of 98% for work that varies from completed assemblies and sub-assemblies to large machined castings and small turned parts.
The 85-employee company is focused on the continual development of ‘lean manufacturing’ techniques and on-going investment, which often exceeds £1 million a year. The company also ensures that staff are kept up to date on company developments and any issues arising.
Managing director Joe Martello said: “We invest in automation and the latest production technology, to help overcome the shortage of the skills that we require.
“However, we still help our own engineers to develop via constant support and training, in order to maximise our return-on-investment and support our customers.”
In the first six months of 2017, Roscomac allocated or spent some £750,000; this included buying a Miyano BNE-51MSY multi-axis turn-mill centre from Bushey-based Citizen Machinery UK Ltd (
www.citizenmachinery.co.uk) — and ordering two further Citizen CNC sliding-head turn-mill machines.
These are a Citizen L20-VIII LFV (LFV referring to low-frequency-vibration cutting technology) and a top-of-the-range M16-V — bringing the number of Citizen installations to 14 machines.
Cell leader Sean Keet said: “The operational flexibility of the Miyano BNE has enabled us to significantly reduce machining times and improve overall productivity.”
He says the new machine has replaced existing three-axis machines, adding that the four turning operations plus a separate milling operation previously required to produce a family of 10 aluminium parts have been replaced by just one turn-milling cycle.
“Overall, the average total cycle time per part has been cut from 13min to just 2.5min. Meanwhile, a complex stainless-steel component that was previously produced using three operations and taking 11min is now made in a single 4min cycle.”
Production flexibility
The BNE-51MSY, which has a 51mm bar capacity, was specified with high-pressure coolant, a Kid 80 bar-feed unit, a ‘hybrid chuck’ and the latest Citizen UK-developed Wizard programming aid. This machine is capable of cutting with three tools simultaneously — overlapped at both ends of a workpiece.
The fixed-head 15kW main spindle and two-axis 7.5kW secondary spindle have a maximum speed of 5,000rev/min and can be synchronised with both 12-station all-driven turrets. Capable of undertaking heavy-duty drilling and milling cycles, each driven-tool position has a 2.2kW drive delivering 25Nm of torque and speeds up to 6,000rev/min.
Cell supervisor Warren Harris said: “The configuration of the three-axis and two-axis turrets gives us the ability to develop applications; it also gives us room to add tool-holders, allowing us to undertake operations such as in-cycle deburring.”
As for training, he says that two operators were sent for initial programming training at Citizen Machinery UK; this was followed by further in-depth training two months later, when they had gained experience of the machine and its operation.
“Even now, if we have a question or problem, we text or e-mail the application team, and they quickly come back to discuss the issue and talk us through it.”
A family-owned business, Roscomac was set up in 1976 on an industrial estate comprising 21 units that were owned by Joe Martello’s father Fernando, who is still involved with the company.
The company grew so fast that by 1999, sub-contract production filled 20 of the 21 units. The site was subsequently sold, and the current 43,000ft
2 factory on a two-acre site in Worthing was set up; in parallel, the company introduced lean manufacturing — along with a policy of continuous investment in automation.
Moreover, climate control has recently been installed across the factory (this is set to maintain a constant temperature of 22°C), and planning permission has been granted for a 3,800ft
2 extension. This will be added next year, along with a new roof over the current facility.
Today, Roscomac runs some 50 CNC machine tools, including 14 Citizen CNC sliding-head turn-mill centres, a 104-pallet FMS and 17 machining centres.
These machines are involved in supplying various sectors, including medical (20% of the £6.5 million turnover), aerospace (12%) vacuum technology, oil and gas, motion control, hydraulics and nuclear.
Focused partnerships
Mr Martello has adopted the same working relationship with his machine tool and equipment suppliers as most of his long-term customers maintain with Roscomac, which means that his key equipment is only bought from a small group of ‘partnership’ suppliers.
Citizen Machinery UK (formerly NC Engineering) has been working with the company since 1990; in that time, it has installed 16 sliding-head and two Miyano fixed-head turn-mill centres. Two more Citizen machines are currently on order.
Mr Martello said: “As our relationship with customers is built on support, quality and on-time supply, our suppliers — such as Citizen —are in the same category, providing leading technology developments that will keep us competitive.
The pending installation of the Citizen L20-VIIILFV is a classic case — it will take us to a level of manufacturing capability that few competitors will be able to match for some time to come.”
Mr Martello has a policy of keeping all staff updated regarding the business, and every three months — together with key employees — he makes a presentation to ensure that everyone has full knowledge of the current situation.
There are also live screens around the factory area showing current workloads, along with the status of work-flow, target dates and actual delivery dates achieved. “This keeps everyone aware and involved. It also draws comment and constructive suggestions for improvement.”
Integrated laser cutting
Citizen Machinery’s laser processing — fully integrated in the turn-milling cycle of its sliding-head turn-mill centres — gives almost endless possibilities for creating geometric shapes or precision holes, whether in solid bar material that has been pre-drilled within the same production cycle or tube.
This development allows the production of burr-free holes (as small as 0.2mm in diameter) and features such as spiral cuts with a 0.025mm kerf width, while maintaining consistent and accurate radii (less than 0.1mm) in corners of slots without any risk of tool wear or breakage.

Moreover, these features can be produced far faster than can be achieved by a separate EDM process, for instance.
The Citizen Cincom breakthrough allows the introduction of new design concepts, particularly in sectors such as medical, electronics and the ‘micro industries’.
Laser cutting offers quick and accurate ‘swarfless’ cutting, the minimisation of any chance of material deflection due to cutting-force reaction, and the highly precise production of special shapes and forms.
The laser system has a separate control and amplifier unit connected to the machine’s Cincom control, which applies
M-code ‘on-cut’ and ‘stop-cut’ instructions. With bar material, standard soluble-oil coolant can be pumped at 70-bar pressure through the bore of the material.
This flow of pressurised coolant ensures a cool cutting condition, washes away any melted material and stops the laser beam from damaging the opposite wall.
In a demonstration, a workpiece produced from 18mm-diameter tube with a 16mm bore was turned and faced, and a single flat was milled on the outside diameter.
The laser beam then proceeded along and around the periphery, using C-axis rotation to create a series of rectangular features that were interlocked, allowing the component to extend and retract.
A series of cuts were then made to form a mesh, and the Citizen logo was profiled around the circumference.
As a result, once the component was finished and parted off, one end was able to slide axially over a short distance while still being interconnected to the main body.