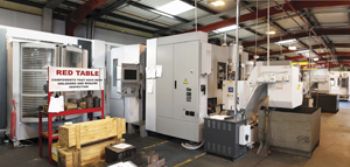
Clitheroe Light Engineering, a family-run sub-contract machinist employing 35 people, has invested £1.4 million in a second flexible manufacturing system (FMS) at its factory in Clitheroe, Lancashire, to cope with continuing high levels of business growth.
The latest installation consists of two DMG-Mori Seiki four-axis machining centres served by a Fastems
(www.fastems.com) automated storage and retrieval system that houses multiple machine pallets and fixtured workpieces. Both systems work round-the-clock seven days a week, machining a diverse range of materials — from brasses and aluminium through to steel and stainless steel.
The sub-contractor is a good example of a small to medium-size UK enterprise that is prepared to invest a large proportion of its operating profit in its manufacturing plant to position itself as a world leader in lean production. Managing director Helen Meloy says: “We started installing our first FMS in 2006 and completed it in 2010. By that time, the original Fastems pallet store had doubled in size and the fourth and fifth machining centres had been added, bringing the total investment to £2.6 million.
“However, as fast as we upgraded the system, our customers in the mining and construction sectors gave us additional work to fill the capacity. Rather than extend the first system, we decided to add a second, separate FMS. Our main customers are global players that can choose to have their price-sensitive components made anywhere, such as Eastern Europe or the Far East, so we have always placed a firm accent on automation to maintain our competitiveness.”

Commissioned at the end of January 2012, the second FMS comprises a pair of DMG-Mori Seiki NH5000 twin-pallet horizontal machining centres with 240-tool magazines; the machines are linked by a Fastems computerised store that holds 20 500mm-square machine pallets on two levels and delivers them automatically to the machines.
An operator fixtures components onto pallets and subsequently removes finish-machined parts at a workpiece load/unload station equipped with a rotating table. Safety is ensured by swing-out double doors and a vertical rolling shutter that isolates operators from the three-axis CNC stacker crane that runs along a rail inside the store. The mast of the crane carries a load-handling device that docks to a repeatability of ±2mm to effect pallet transfer into and out of each storage position and on and off the outer pallet position of the twin-pallet machine tools.
System software
Fastems MMS software oversees FMS operation. Running on a standard Windows-based PC, its main tasks are to control the stacker crane and schedule automatic pallet transfers between the load stations, store and machines. The main window of the control displays a mimic of the entire system, using colours and icons to show the real-time status of all main FMS elements.
When a pallet is sent from the load station into the system, a ‘manufacturing route’ defines its flow through the FMS and ensures that the correct NC program is downloaded over a DNC link to the appropriate machine and initiated when the pallet arrives. The MMS software has information not only on the NC program to be loaded but also on the component and fixture, as well as the tools needed to complete the job. If the intended machine is not available — for example, because it already has work waiting on the second pallet or because all the required tools are not in the magazine — the pallet is routed to the other machine, if it is available, or else into store.

To automate the often difficult and time-consuming task of managing tools, ‘virtual’ versions of the 240-tool magazines serving the NH5000 machining centres are held in the Fastems control, which includes data on the remaining life of each cutter. Available tools, as well as those that need to be added and/or removed for any given job or series of jobs, can be evaluated. Even tools stored outside the magazines are included.
Performance data and statistics of stacker crane operation are available and the production reporting interface generates information such as the total machining time of a particular order. The operational modes of the machine tools are also tracked in a database, providing information covering on-line/off-line status, ‘cycle on’, ‘feed on’ and errors/alarms, all of which can be interrogated remotely.
Economic batches
The efficiency with which a mixed schedule of work is presented to the two spindles means that small batches can be produced very economically. For example, Clitheroe Light used to machine batches of 120 manifolds for a customer that wanted 10 per month and then deliver them in 12 instalments throughout the year, absorbing the financial cost of the consignment stock. Now, it is economic to run off 10 components and deliver them straight away. Even single items can be produced cost-effectively.
When Clitheroe Light installed its first two Daewoo (now Doosan) twin-pallet four-axis HMCs, it achieved significant reductions in labour costs and lead times, as well as improved cash flow. Parts could be set off-line, presented to the spindles more promptly, machined in a shorter floor-to-floor time and invoiced more quickly. In 2004, the sub-contractor moved further ahead with automation by retrofitting a seven-pallet pool to one of the machines — an HM500.

Two years later, the company embarked on its first FMS by positioning the other twin-pallet Daewoo — a 400mm pallet HC400 — alongside two new Mori Seiki NH5000s with 500mm pallets. A Fastems store with two load/unload stations was purchased to feed the three HMCs automatically with pallets (36 pallets were held on three levels). Several aspects of this installation are noteworthy. One is that dissimilar makes of machine tool are accommodated by the FMS, and that different sizes of pallet — 400 and 500mm — can be accommodated (components fixtured on any of 36 Wixroyd Zero Point sub-plates can be directed to either of the Mori Seiki machines, while 12 of the sub-plates can also be sent to the Daewoo).
Another point to note is the ability of such systems to be expanded as business demands dictate. In Clitheroe Light’s case, the 17m-long Fastems store was doubled in length to house 72 machine pallets, while a fourth HMC was added in 2009 and a fifth in 2010; both were DMG-Mori Seiki NH5000s with 240-tool magazines, although any make of three-, four- or five-axis machining centre could have been added.
It is Clitheroe Light’s intention to upgrade the two FMSs further with the addition of an external tool store for cutters that will be freely available (via a gantry exchange system) to any of the seven machines within the two systems. This will further increase flexibility and reduce tooling costs, as fewer cutters specific to particular machines will be needed — and a reduced number of sister tools will be sufficient for unattended operation.