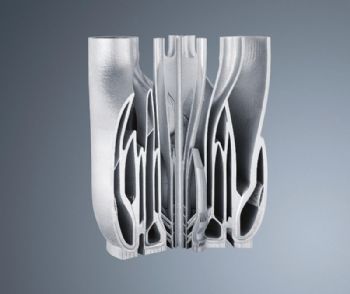
Thanks to an interchangeable-cylinder concept and ‘industry-ready’ peripheral equipment, the new TruPrint 3000 3-D printer from Luton-based Trumpf Ltd (
www.uk.trumpf.com) can undertake the large-scale production of complex metal parts up to 300mm in diameter and 400mm high.
Furthermore, Trumpf says that, when enhanced by complementary process stations, the TruPrint 3000 can become a 3-D printing cell.
This machine uses the laser metal fusion (LMF) technique, in which the laser melts metallic powder layer by layer on a production bed to produce parts.
LMF is particularly suited to the manufacture of geometrically complex and bespoke parts, benefitting sectors that include dental, medical, automotive and jewellery.
Components can be made from any weldable material (in powder form), such as steel, nickel-based alloys, titanium and aluminium.
Since the TruPrint 3000 is equipped with two supply cylinders, up to 75 litres of powder are available for each job, which is around two-and-half-times the construction volume.
This is sufficient to complete an entire manufacturing process without having to stop for refilling. Even if the powder were to run low, the tool-change cylinder would ‘kick in’ (the machine is designed so that the supply and overflow cylinders can be changed without interrupting the manufacturing process).
To ensure consistent quality, an automated sieve station is available; this can refine several hundred kg of powder per hour. Furthermore, grain size, grain distribution and flow are all factored in to determine the optimum laser output and process speed to maximise ‘powder performance’.
The TruPrint 3000 can also be specified as a complete process chain for 3-D printing, with an external unpacking station where parts can be cleaned and detached from the substrate.
Customers not only benefit from the higher machine availability that results from external unpacking, but from a safe and sealed powder cycle (excess material is returned automatically to the sieve station).