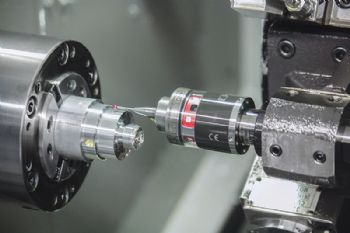
Helmut Christmann GmbH, based in Birkenfeld near Pforzheim, is a sub-contract manufacturer of high-precision parts that are made on a variety of machine types.
CEO Marcus Christmann says: “We turn parts that are just 0.2mm in diameter, and we carry out electrical discharge machining with wire that is just 0.03mm thick; we also mass-produce carbide parts to a contour accuracy of ±0.002mm.
To ensure that we achieve the required levels of precision, we have been long-time users of workpiece- and tool-measuring technology on our machining centres.”
For part measurement, Christmann uses probes from Blum Novotest (
www.blum-novotest.com). These are mounted on tool-holders and fitted into the spindle when required.
The machine then scans the appropriate measuring points, integrating measuring tasks into machining programmes without needing to unclamp the workpiece.
Based on its good experience with Blum, Christmann again turned to the measuring-technology specialist when the need for in-cycle measurement on a lathe arose.
Because the tools are mounted on a turret in the machine’s working area, the touch probe — a Blum TC54-10 T — remains in the machining area throughout the production process, so it is exposed to chip impacts, as well as shock and vibration.
The probe eliminates the need for external measuring and allows one operator to oversee two machines at the same time.
Christmann also uses Blum’s LaserControl system for tool breakage detection and tool monitoring; it detects (and compensates for) tool wear, while broken or excessively worn tools are automatically replaced.
This machine-integrated laser-based instrument also measures tools at nominal spindle speed and in the actual tool-clamping situation.
This means that clamping errors are detected, and factors such as temperature-related spindle displacement are compensated.