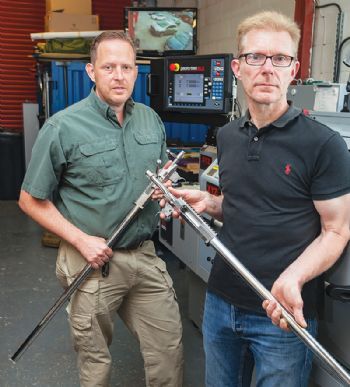
With over 30 years of gun-smithing between them, along with 20 years’ experience of shooting at international level, three friends and business acquaintances — Stuart Anselm (Osprey Rifles), Pete Walker (Walker Custom Rifles) and Gary Costello (March Scopes) — decided to pool their resources to tackle the niche market of bespoke gun-smithing.
They subsequently formed PGS Precision Engineering.
Much of the new company’s work was one-off commissions that did not justify the investment in a CNC machining capability. However, a contract for higher-volume work made upgrading from manual machining a feasible proposition.
Mr Anselm said: “This contract was for machining rifle-barrel blanks. These are already contoured to the final finish, with the rifling machined; our job is to machine the chamber, which is the location for the bullet in the end
of the barrel.
This chamber, which has to be both accurate in terms of size and very precise regarding surface finish, is produced using a chambering reamer.
This was our first contract for 50-calibre military rifles; in addition to finishing the chamber, we also had to carry out the turning and threading required to fit the ‘rifle action’ and the suppressor — more commonly known as the silencer. These increased volumes prompted us to consider CNC machining.”
With regard to machine selection, the barrel blanks come pre-machined, although the bore is not necessarily centred, so a four-jaw chuck would be required.
Furthermore, the necessary tooling requires the ability to pass high-pressure coolant through the spindle from the back of the machine, using a ‘muzzle flush’ device created by PGS Precision.

The lathe selected would need to be capable of machining the 416 stainless ‘barrel steel’ that is popular in gun-smithing — and have a spindle bore large enough and long enough to allow both the coolant system and barrel to be fully enclosed within it.
The company decided to purchase an XYZ SLX 355 ProTurn lathe from Burlescombe-based XYZ Machine Tools (
www.xyzmachinetools.com), because it particularly liked the ease of use of this machine’s ProtoTrak control system — in particular the ‘TraKing’ facility; this allows the operator to manually run through a program using the hand-wheels before pressing ‘cycle start’.
The SLX 355 was also favoured for its ability to be operated as a manual machine; and while 95% of the work would be programmed, the bespoke nature of the products called for manual intervention to achieve the ‘final fit’ that PGS requires.
The ability to combine the ProtoTrak control with manual operation was also a factor in the machine’s selection (with the SLX 355, it is possible to accurately and quickly produce tapers manually).
PGS chose the SLX 355 over the smaller SLX 1630, as its 1,000mm between centres could accommodate longer barrels in the future.
Other aspects of the machine that appealed were the 52mm spindle bore, the 5.75kW 4,000rev/min spindle (with constant surface speed), and the 150mm of tailstock travel (which is used for reaming the chambers).
Mr Anslem says: “The response we got from XYZ was excellent. We took some sample barrels with us for machining trials; we also found machine programming to be straightforward; within half a day, we had full confidence that the SLX 355 would do what we wanted.
Moreover, the support that we knew was available from XYZ in terms of training and service added to that confidence. The machine was commissioned the same day it was delivered, and we had completed our training within the first week.
We then spent a short time manufacturing our bespoke muzzle flush coolant system and were very soon in production.

“We are machining barrels much faster than we ever could using our manual lathes — plus we have the benefit of consistent accuracy and quality.
With the ProtoTrak control, we can also retain an individual customer’s programs; this means that if a replacement barrel is ever needed, we can manufacture it without the customer having to relinquish their gun for a couple of weeks.”
While saving seconds was never a priority for PGS Precision, certain aspects of the SLX 355 are proving beneficial in terms of cycle time.
The company specified the optional four-position auto-indexing tool-post, which PGS normally uses with turning, parting, threading and boring tools.
Mr Walker said: “Adding the automatic tool-post was a great decision, as we can complete the turning and threading cycles in under 3min; we couldn’t hope to get anywhere near that with a manual system.”
Since installing the SLX 355, business has developed for PGS, and the company is moving to larger premises next to another gun maker.
This move will see collaborations, volumes increasing, and the need for additional machining capacity — both milling and turning.
The plan is to have one SLX 355 dedicated to turning and threading, and a second specifically for the chambering operations — plus an XYZ ProtoTrak mill for milling work.
In conclusion, Mr Walker said: “Given our relatively low volumes, we need a control that is quick and easy to program. The ProtoTrak system is perfect for our needs, making the transition from manual to CNC very straight-
forward.”
In-house machining
Over 30 years ago, Gordon Robinson formed D&D Engineering (Hull) to design, develop and manufacture bespoke conveyor systems for the food-processing industry. However, he did not machine parts in-house; he relied on local sub-contract manufacturers to provide the components he needed.
This approach worked perfectly well in the company’s formative years, but it all changed when Mr Robinson was joined in the business by his son — and current managing director — Mark, who had plans to significantly grow the business.
Within seven years, D&D had outgrown its original premises, and the company decided to buy land and create a purpose-built factory.
Mark Robinson says: “It was a risk when we mortgaged to buy our current premises, but with the business growing, it was one that paid off quickly; we repaid the 25-year loan in just 12 years.”
This success came not only from the increased sales of conveyor systems but also from bringing machining in-house for its own production; that allowed the company to also undertake sub-contract machining — and to develop it as a major part of the business.

D&D first introduced a turning capability in the form of SLX ProTurn lathes with the ProtoTrak control. Mr Robinson says: “We found this control very easy to use, and an ideal first step into CNC machining.”
With this initial investment satisfying the then current turning requirement, attention turned to milling — and the purchase of ProtoTrak-controlled SMX bed mills.
“This control makes producing contours, pockets, holes and a host of other features on parts for our conveyor systems so easy.”
With the business continuing to grow, both for its own products and sub-contract machining for customers in a variety of industries — including wind power, offshore oil and gas, petrochemical and food — D&D looked to develop its machining capability further and installed two XYZ MiniMill 560 vertical machining centres.
With Siemens CNC systems and fourth-axis attachments, D&D was able to take on larger batch sizes. Moreover, Mr Robinson says the Siemens control is “perfect for our business, and it makes programming at the machine easy.”
The additional business generated by having the MiniMills meant that D&D was able to buy more machines: an XYZ 1020 VMC was closely followed by a Compact Turn 52 and a 250 TC from XYZ.
The subsequent installation of an XYZ XL 1100 lathe with 2m between centres and an 1,100mm swing over the bed took care of larger-diameter turning needs.
“Many of our machines are now running 18hr a day, so we ensure that they are regularly serviced. Those that we are most dependent on have XYZ service contracts,” added Mr Robinson.
While the ProtoTrak and Siemens controls make shopfloor programming a relatively simple procedure, thanks to their conversational languages, D&D has also invested in off-line programming from XYZ.
“This is opening up new opportunities, especially in the injection moulding sector. With this mould tool work came a need for further investment, this time in a large-capacity VMC — an XYZ 2010 HD.”
Part of XYZ’s heavy-duty range of machines, the 2010 has a work envelope of 2,000 x 1,000 x 800mm and features hardened box slideways, with six slides alone on the Y axis. D&D uses the 30-position tool-changer to maximise the run time, and it runs the machine unmanned overnight on long-cycle-time work, switching to shorter runs during the day.
In conclusion, Mr Robinson said: “One knock-on effect of our investment in XYZ machines has been us starting an apprenticeship scheme several years ago; we currently have five apprentices in our workforce of 28, and this is something that we are very proud of.
More positive is the fact that many of those we have trained stayed with us and have gone on to operate and program the XYZ machines.”