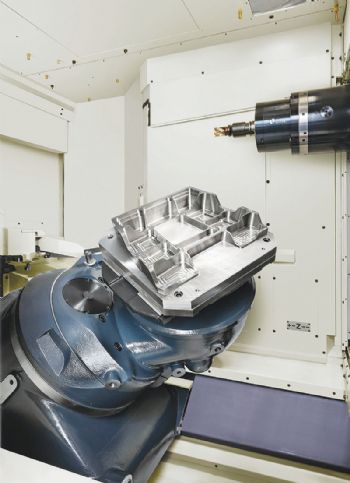
A new addition to the Makino family of five-axis machining centres is now available from Thames Ditton-based NCMT Ltd (
www.ncmt.co.uk) — the UK and Ireland agent for the Japanese manufacturer.
With a working volume of 730 x 750 x 700mm, the a500Z horizontal-spindle model features a rigid structure and low inertia, which are said to “endow it with a production efficiency similar to that of a four-axis machine”.
A one-piece base casting, slant-bed design and three-point support offer high levels of stiffness and stability, while the swivelling table has a minimum of overhang; high levels of positioning accuracy are aided by the short distance between the A-axis pivot point and the workpiece.
Also ensuring a high level of precision is the machine’s thermally symmetrical structure; this is combined with heat removal from the 303Nm HSK-A63 Makino spindle and core-cooled ballscrews.
Furthermore, the direct-drive motors on the rotary axes are fitted with cooling jackets.
Meanwhile, the ability to use ‘inertia active control’ during simultaneous five-axis metal cutting allows users to accelerate and decelerate workpieces up to 630mm in diameter, 500mm high and weighing up to 400kg.
Additionally, the standard automatic tool changer accommodates up to 60 cutters and achieves a chip-to-chip time of 2.4sec.
With regard to chip and coolant control, unlike conventional five-axis trunnion table set-ups, the a500Z has a wide trough located beneath the table.
Coolant flow from a washing system that encompasses the pallet loading area prevents chips accumulating by ensuring that they fall directly into the trough.
The machine’s Makino Professional 6 (PRO 6) control includes Geometric Intelligence (GI) motion control.
To highlight the potential benefits provided by this capability, GI Drilling enables the spindle and tool to follow an arc from hole to hole instead of moving along linear paths, thus reducing non-cutting times.
Similarly, GI Milling is designed to improve 2-D profiling performance by letting the user define a tolerance on each corner-milling path.
Automation is available for both pallet and parts handling, including the MMC2 and VIP, which use six-axis robots. Standard automation systems available on the market can also be integrated with the machine.