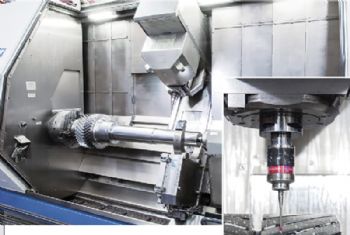
Schuler AG (
www.schulergroup.com) provides presses, automation solutions, tools, process know-how and services for the metal-forming industry.
Its customers include automotive manufacturers and their suppliers, as well as companies from the forging, household equipment, packaging, energy and electrical sectors.
At Schuler, integral gears on large-press drive shafts had historically been produced using special gear-cutting machines; and while the latter achieved a high level of repeatability, it took a considerable time to manufacture a driveshaft.
Shaping the gears alone took 16-19hr, while moving parts that weigh nearly 700kg between the various processing machines further extended and complicated the production process — and caused a bottleneck.
To improve productivity, Schuler installed a modern turning/milling machining centre that could complete shafts in a single set-up, including the machining of gears using a specially manufactured profile cutter.
Furthermore, to reduce handling and improve both quality and consistency, the company decided to carry out all necessary measurements on the machine.
Thomas Vujica, from Schuler’s production planning and NC programming department, said: “Previously, we had no way of directly measuring the form deviations of the tooth flanks, although this wasn’t necessary with the gear-cutting machines, because they are constructed in such a way that there is always an involute.
“The question of measurement only became an issue when gear production migrated to the turning/milling centre.”
To start with, Schuler sent the heavy driveshafts to another company to be checked on a special measuring machine. However, depending on order backlogs, this process took two to three weeks, negating any time advantage provided by gear milling on the machining centre.
The solution to Schuler’s predicament came in the form of a TC64-DigiLog touch probe from Blum-Novotest GmbH, which has a UK subsidiary in Burton on Trent (
www.blumnovotest.com).
The advantage of the DigiLog touch probe is that it can carry out both digital measurements and analogue scans, so it can be guided over a surface and register measurement data continuously.
The complete measurement of a gear wheel consists of 144 individual measurements on a slanted track along the whole tooth flank. This includes 36 teeth with two flanks each in both halves of the double helical gear.
However, the complete measurement procedure takes just 13min at a scan speed of 1.8m/min. During this time, the probe records 570,000 individual measurement values (only the linear axes are used during the scan, as this excludes any errors of the rotation axes used for production).
Software developed by Mr Vujica generates a report that includes diagrams; this provides a simple means of establishing whether there are deviations from the ideal form and — if so — how big they are.
The machine operator can keep track of the measurements on a PC as they are generated — and differentiate between “outliers caused by impurities” and genuine quality issues. Also, the automated measurement technique avoids errors associated with manual measurement.
Use of the DigiLog probe means that production is now backed up by reliable quality assurance and that delivery times are significantly shorter. In fact, Schuler can now manufacture and dispatch a driveshaft within a single day,
if necessary.
In conclusion, Mr Vujica said: “The co-operation between Blum and our production and software departments has been excellent.
"We developed the measuring sequence together, optimising it steadily and integrating it into the production process. Thanks to the DigiLog touch probe, we now have very fast and reliable manufacturing — and we no longer have to rely on the old special gear machines.”