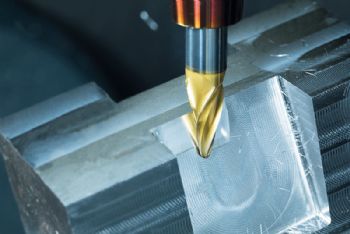
The new 3D Finish milling cutter from Sheffield-based WNT (
www.wnt.com) — part of the Ceratizit Group — is said to reduce the time required for finishing operations performed on five-axis machines, while simultaneously improving surface quality.
A development of the ball-nose end mill, 3D Finish has been designed with a large radius in the cutting area; this allows the cutters to achieve increased step-overs compared with conventional ball-nose tools with the same tool diameter.
As a result, processing times for pre-finish and finish machining operations are reduced by up to 90% — without the workpiece, tool and machine being subjected to a higher load.
According to WNT, 3D Finish cutters also accommodate greater widths of cut without compromising surface finish. For instance, a typical 20mm-diameter ball-nose cutter would achieve a surface quality of Ra1.6 with a step-over of 0.5mm, but with the 3D Finish and its large radius, the step-over can be increased to 6.93mm while achieving the same surface quality.
3D Finish tools — available in barrel, oval, taper or lens shapes — are suitable for the five-axis finishing of free-form surfaces, such as those found in tool and die production, as well as aerospace workpieces.
The cutters are available in a variety of sizes and styles and can be specified for machining steel, stainless steel, cast iron, non-ferrous metal, heat-resistant steel and hardened steel.
In assessing the cost-effectiveness of 3D Finish tools, machining experts at the Ceratizit Group carried out extensive trials to highlight the time savings that can be achieved when compared with a conventional 10mm-diameter ball-nose cutter.
In the trial, a 100 x 200mm component was milled at a feed of 200m/min. With a step-over of 1.5mm for the 3D Finish cutter (compared with 0.1mm for the ball-nose tool), the total milling travel was reduced from 200m to just 13m, with a corresponding reduction in cycle time from 79 to 7min — along with a reduction in machining cost of 88%.