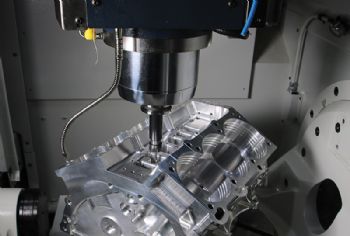
Alitech Precision — located in Silverstone, just a short walk from the world-famous racing circuit — is a sub-contract design, ‘concept delivery’ and manufacturing company that specialises in the motor-sport industry.
When the company bought its first five-axis machining centre, it needed a CAM system to ‘drive’ this latest purchase and selected software from Bicester-based Open Mind Technologies (
www.openmind-tech.com).
Alitech started just three years ago with a Haas VF2SS machining centre and a three-axis CAM package. As the business grew, it bought another two Haas machines — a VF4SS with a fourth-axis rotary table and, more recently, a Haas DM2 high-speed machining centre.
While the three-axis CAM package had served the company well, it had limitations programming four-axis machining — and it could not cope when Alitech installed a Spinner U-620 simultaneous five-axis vertical machining centre, necessitating the upgrade to Open Mind’s HyperMill CAM software.

Specialising in the design of motor-sport solutions and taking concepts through design to manufacture in the shortest possible time, Alitech works with a wide variety of customers in the vicinity, which is commonly referred to as ‘motor-sport valley’.
Managing director Darren Cudd says: “We tend to be the company that customers call when they have left releasing designs for manufacture a little bit late.
“We step in and make sure that parts and vehicles are ready to go, whether they are for the road, the test track, the race circuit or F1 teams. Service and response times are critical to our business, which is why we invest in high-end technology like HyperMill.
“We knew from the outset that we would be using our Spinner machine for simultaneous five-axis machining rather than positional five-axis cutting, so when we looked for a new CAM system, we narrowed our selection down to three possible suppliers, finally selecting HyperMill for its five-axis capabilities.
“Moreover, standard features in HyperMill were chargeable bolt-ons with other suppliers.”
Installing the U-620 Spinner machine necessitated a new CAM system, but Alitech was already intent on acquiring a high-end one.
Mr Cudd says: “While our previous three-axis CAM system worked reasonably well with our existing Haas machining centres, when machining complex parts such as a cylinder block, we needed to be sure that the program was correct before loading the job on the machine.
With our old system, the simulation and collision detection were not really at the level we needed; after spending well over 100hr on design and a similar time on programming, we needed total confidence.

Putting so much time into an engine block but not being confident in the anti-collision credentials was itself enough to justifying buying HyperMill — and programming times have been cut by at least 50%.”
Referring to collision detection and avoidance features, Mr Cudd says: “We recently machined — from billet — a turbo manifold for a motor-sport customer. This part required two 40mm-diameter oval-shaped curved port holes some 200mm deep.
“We used an 8mm diameter ‘lollipop’ cutter protruding 70mm out of a slim heat-shrink tool-holder. HyperMill modelled the complete work envelope and detected the collision parameters for the cutting tool, tool-holder and machine spindle.
“By precisely simulating the process, we are running at high speed — even though the heat-shrink holder is often as close as 0.25mm to the port walls during machining.”
This collision detection feature also works in conjunction with the software’s Z-level finishing cycle, and it allows Alitech to run short-length cutting tools in port bores.
This capability results in improved stability and surface finishes, while allowing machining at higher speeds and feeds.
“Before using HyperMill, we were turning away particularly challenging projects, as we couldn’t achieve the lead times required. This has now changed.
“One customer required a billet inlet manifold for a drag racing car in just two weeks. Within this time-frame, we used a Romer arm to capture the engine co-ordinates, load them into our CAD system and reverse engineer a complete solution.

“The manifold required six parts to be designed, manufactured and delivered in two weeks. Without our use of HyperMill, this would have been impossible.
“For us, the system’s port-machining cycles are a major benefit, as we design and manufacture a lot of inlet manifolds, valve seats and inlet ports for cylinder heads. HyperMill helps us to machine down and around corners; it is also easy to use — and as close to ‘click and go’ as you can get.
“Furthermore, the stock model tool allows us to simulate what stock is remaining on the component at any point in the process. This is really useful for parts that require second operations.
“If we have to re-orientate and re-fixture a job, HyperMill shows us exactly what stock remains on the job and what has been removed, allowing us to eliminate air cutting while preventing us from hitting a job too fast or hard with the tools — or having a collision.
“This capability gives us significant time savings in set-up, programming and machining on very complex jobs that may need multiple set-ups.”