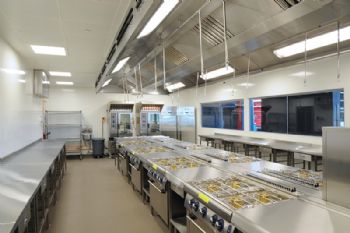
Shine Food Machinery has been trading for over 40 years; over the past 10 years, it has supplied catering equipment worth more than £100 million to customers ranging from small cafes and schools to the Ministry of Defence — all delivered from its headquarters in Newport.
Senior design engineer Neil Thorne says: “When we win a contract, we use SolidWorksto design the individual components for the kitchen — such as the extraction systems, tables and servery counter.
“Once the client has approved the design and site dimensions have been taken, we send the manufacturing drawings to the factory floor.
“The components are nested, laser-cut, folded, welded and assembled; and once the finished product has been inspected it is delivered to site to meet the installation date.”
With each job being bespoke, Shine makes of different components a year, each requiring its own CNC code. For example, a full servery counter could have 200 different components.
The company uses Radan’s Radraft, Radprofile and Radnest (
www.radan.com) to cut every sheet-metal product using a Bystronic Bysprint 3015 3kW laser.
Mr Thorne says: “It is very important that the parts we make are accurate and within tolerance; otherwise, we will encounter problems at the assembly stage. We find that Radan ‘flat patterns and nests’ the components extremely accurately from SolidWorks.”
Despite the high level of accuracy and nesting efficiency achieved using Radan, Shine came across an issue resulting from design constraints and human error.
“For aesthetic reasons, we can’t have neighbouring cabinets with the grain on the top going in different directions — it all has to go the same way.
"This was a problem, because when the project was going into Radan, the software was nesting in the best orientation for sheet utilisation. We needed to overcome this without having to nest everything manually.”
Following discussions with Radan’s brand manager Olaf Körner and software developers, a macro to solve this issue was created specifically for Shine. Mr Körner said: “As a company, Radan was challenged by this requirement of Shine’s.
“The high volume of parts in a project and the high-quality materials used required a highly automated — and very reliable — process.
“With input from the engineers at Shine, we put a process known as ‘F-Stop’ in place; this allows Shine to produce the kitchens with a minimum risk of costly errors.”
At the design stage in SolidWorks, a 5mm letter ‘F’ is put on the top face of the panel, to indicate the correct grain direction. Mr Thorne says: “Thanks to the macro, when Radan is ‘flat patterning’, it determines from the F-Stop which is the top surface and which way the grain has to go.
"Radan then nests with the correct top face and the grain going in the right direction, rather than purely optimising sheet usage.
"This is extremely important for the aesthetics of our installations — and it stops issues on the factory floor.
"Previously, parts could be nested either in the wrong orientation or upside down, and even folded the wrong way in the press brake, resulting in them being scrapped.
"The amount of scrap we produce has reduced dramatically.” Following the success of the F-stop macro developed for Shine, Radan is now working to include this feature in a future general release of the software.
Shine has also seen huge time-saving benefits from the standard features of the Radan software.
Mr Thorne says: “From drawing approval from the client to getting our products to site requires a fairly quick turn-round, so as soon as the drawings are approved we need to get programs to the factory floor as quickly as possible, which Radan allows us to do.
“Flat patterning for a big contract such as a school would previously have taken a few days; it now takes just 45min.”
Although the volume of scrap produced has been largely reduced, Radan does allow these remnants to be optimised. Design engineer Steffan Owen says: “For offcuts, we use the Remnants feature.
Our scrap used to go in the bin, but now every offcut is put back in the system; and the first thing Radan does is to look at a remnant first rather than use a new sheet — and using the Projects and Labelling functions has further increased efficiency.
“Projects allows us to know where everything is; and with Labelling, all parts are marked automatically, which is crucial for identifying which components are for what job, what the contract is, and what the item number is.
“Previously, the labels would be handwritten for every part, which was time-consuming — particularly as contracts can have well over 1,000 individual parts.
“Labels are now printed automatically; our laser operator simply peels them off and puts them on the appropriate part.”
The increase in efficiency and production rate in the cutting operation has introduced a need for further investment to alleviate a bottleneck at the bending stage. Shine will shortly be installing a third press brake.