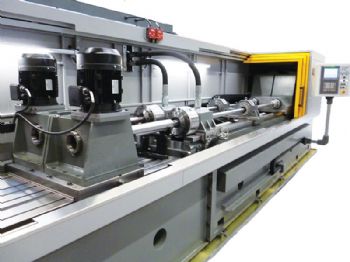
The BTA self-piloting drilling process can machine bores from 18mm in diameter with length-to-diameter ratios of up to 100 or more.
That said, Chessington-based deep-hole drilling specialist Mollart Engineering (
www.mollart.com) provides application engineering support involving drill heads up to 1,000mm in diameter (together with its German tooling partner Botek).
Chris Barker, Mollart’s director of tooling, says: “The BTA drilling process originated from the Boring and Trepanning Association, which was formed by a group of European manufacturers in the 1940s.
"The BTA process — also known as the single-tube system or STS — covers deep-hole solid drill heads, pull-boring and counterboring heads, step and form boring tools and trepanning heads.”
These different tool head types — each providing a more effective deep-hole production solution than conventional drilling and boring — need to be appropriately configured and applied to achieve optimum results, which is why Mollart Engineering formed its BTA Application Centre.
This is based in Chessington, but there are also regional specialists in the Midlands and the North of England — the latter providing direct support to customers in Scotland.
Mr Barker says: “Due to its configuration and hole size capability, BTA drilling requires more power than gun-drilling; and while both drill from solid, using high-pressure coolant to directly lubricate the cutting zone and evacuate chips away from the head of the drill, there is a marked difference in the design of a gun-drill and a BTA tool.
Gun-drilling uses a solid-carbide tool head brazed to a tube, through which coolant is pumped under pressure to the cutting edge of the tool head.
Chips are evacuated via a deep V-shaped flute in the drill head extending back along the exterior of the tube between the drill and the drilled portion of the workpiece.
“The BTA system has a rigid drill head — with either brazed solid-carbide or indexable inserts — that is secured to a support and feed tube.
"Coolant is pumped under pressure to the cutting edge between the outside of the tube, the cutting head and the newly created bore in the workpiece material.
"This pressure forces the chips to be flushed back through the drill head, tube and machine spindle to be collected. In both BTA and gun-drill systems, guide pads in the drill head support the cutting action, enabling continuous feed rates to be applied straight, and round accurately sized holes with high degrees of surface finish to be achieved.”
Machining stability
Mr Barker goes on to explain that because chips are evacuated through the internal bore of the BTA drill head and tube, fluting or grooving is not required; this provides a greater cross-section of tool that increases rigidity and hence stability under cutting conditions.
Meanwhile, pull-boring is a BTA-based process used to accurately enlarge existing through bores to maintain — for instance — a constant wall thickness, tolerance or surface finish.
The process uses a tensioned BTA boring head but with the wear pads set ahead of the cutting inserts, so that the cutting tool can be pulled back through the workpiece.
Counterboring is an effective use of BTA technology to open up existing pre-bored holes. Here, the BTA drill head can achieve a more-precise diameter or concentricity of a bore — or provide an additional feature such as a bearing or oil seal diameter.
While gun-drilling can be used to machine bores as small as 0.5mm in diameter, BTA holes start at 18mm due to the size required for the drill tube; and as mentioned earlier, the use of trepanning-style heads extends the BTA concept to bore diameters up to 1,000mm.
The trepanning operation also produces a central core of material that can be used to make further components, and it is particularly economic when processing high-value materials.
BTA drill heads are larger in diameter than the rigid tube into which they are screwed.
Moreover, the construction of the tool means it can be used for drilling difficult materials such as exotic alloy steels and stainless steels — and at penetration rates several times greater than conventional drill types.
The BTA system is now widely used by the oil and gas, nuclear and defence sectors, as well as general engineering.
Recent applications at Mollart Engineering have featured the use of the Acubore deep-hole drilling centre at its Chessington sub-contract facility, to produce 63.5mm-diameter bores from solid in Super Duplex stainless steel (13% chromium), using BTA tooling technology.
These oil industry components were produced from bar material 250mm in diameter x 2,180mm long and weighing some 900kg.
The Acubore machine has been designed to allow both on-centre-line and off-centre drilling using gun-drills and BTA tooling — or a combination of both.
This flexibility allows the use of the drilling process that best suits the workpiece and the level of accuracy required.
The Acubore machine, which was developed by Mollart, has a 30kW motor (up to 666Nm of torque) and a maximum spindle speed of 5,000rev/min.
This enables the machine to produce both large- and small-diameter holes, while having the power to drill exotic materials and the speed for freer-machining materials.