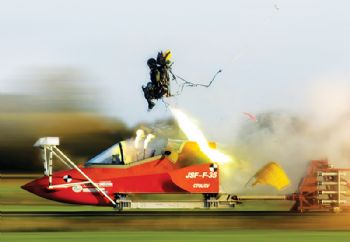
Middlesex-based Martin-Baker has been the world leader in the design and manufacture of aircraft ejection and ‘crashworthy’ seats for over 70 years (
www.martin-baker.com).
During that time, the company’s seats have saved over 7,500 lives, and it has received 11 Queen’s Awards. Its latest designs offer unprecedented life-saving capabilities, and there are over 17,000 of its seats currently in service.
The company supplies ejection seats for 56 different aircraft, plus spare parts for seats still in service dating back to the 1970s.
In addition, seat requirements can differ for the same aircraft (Martin-Baker supplies more than 90 airforces, with the seat specification depending on factors such as the terrain the aircraft is to operate over and the aircraft seating configuration).
The complexity and variation of the eats result in a large number of specialised components. Rupert Hanak, head of production engineering at Martin-Baker, highlights the difficulties the company needs to overcome for efficient production.
“We have thousands of different components and batch sizes are often five to 15 parts. The length of each production run is too short for us to develop faster cycle times, so the key objectives are an extremely quick change-over time between different parts, along with process reliability so that we know they will be ‘right first time’.
We are consistently achieving over 80% OEE — Overall Equipment Effectiveness — on a 24/7 basis with the technology we are using.”
At the heart of Martin-Baker’s production is a manufacturing cell comprising four NHX 4000 2nd Generation horizontal machining centres from Coventry-based DMG Mori UK (
www.dmgmori.com); each machine has 240 tools, and the machines are connected by a linear pallet pool (LPP).
This system has 70 pallets and supports 500 different ‘live’ parts.
A VIO tool pre-setter is linked to the machines and downloads the tool-setting data. Martin-Baker has a core of around 200 standard tools, which the CNC programmers have to work with.
The production schedule is controlled from Martin-Baker’s SAP system, which displays a list of the next four weeks’ worth of jobs to be completed on a terminal on the LPP.

The engineers can then use their experience to select the order in which the jobs should be run, picking long-running safe parts for the unmanned night shift and more challenging work for the day shifts.
Mr Hanak added: “We use Mori Messenger in the office to monitor machine activity and gather metrics. The system shows the run rate of the machines and displays alarms.
“I can then drill down into the data to find the problem, which could just be machine loading and work availability, or tooling problems such as swarf wrapped around the cutter. We can then take action based on the data. Essentially, all our decisions are data-driven.”
Within the software solution, SAP knows the work-holding requirements of each job, the machining time and the tooling. Linked to the LPP system, the correct combination of pallet and fixture is then presented to the engineer for loading.
Extra software supplied by DMG Mori detects broken tools and tool ‘out of life’ situations, ensuring that a job requiring the faulty tool is not loaded to the machine and automatically cutting another job from the work list, while the problem is remedied. The system can also recognise sub-locations on a pallet and skip over these, if no material has been loaded.
“We have had a considerable amount of applications support from DMG Mori to tailor the systems to our requirements; we also have one of the company’s engineers on site permanently to ensure the smooth running of our machines and to fully maintain them.”
Martin-Baker currently has 22 DMG Mori machines, rising to 23 with the pending installation of another NMV3000 DCG with 32 pallets.
These five-axis machines can combine multiple operations. One of them is used to produce a family of rocket motor end-cap parts, running one manned shift and 16hr unmanned, yet still achieving 80% OEE.
“With a five-axis and a turning capability on one machine, we can go from raw material to finished part in one step. We used to sub-contract some of the parts we now put on the NMV3000 DCG.
By making them in-house, we now have more control over security of supply.
“Additionally, completing each job on one machine eliminates the complexity of multiple operations and reduces the chance of something going wrong.”
Martin-Baker also has a range of DMG Mori NTX, NT and NL turning centres. For these, the rationalisation of bar sizes minimises change-over times between different parts; and even when the bar needs changing, this is achieved within 15min.
Innovations added by DMG Mori include special part conveyors for the safe unloading of critical components that must not have any surface imperfections.
One of the NL machines is even used for machining solid rocket fuel and has been heavily modified to ensure safe operation in a separate room.