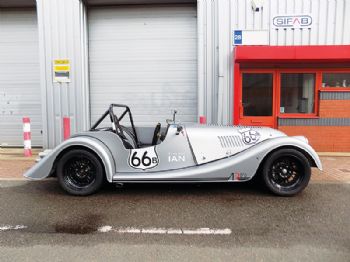
After many years of working for others developing and building race- and championship-winning cars, particularly in the ‘classic’ and ‘modern classic’ sectors, Simon Hall — with encouragement from many of his contacts — decided to work for himself and formed SiFab Engineering Solutions.
Mr Hall said: “Based on promises of work, I decided to set up the business in 2015. Initially, I focused mainly on fabrication, producing and retailing a large range of ‘performance products’ for small-volume manufacturers such as Morgan, TVR and Ginetta.
“These products — such as radiators, fuel tanks, brake and suspension components — are designed to help transform a road car into a racing car.
“However, I was having to rely on sub-contractors for any machining work; and while initially this was the sensible thing to do, it did have its drawbacks — including having to over-order to get reasonable response times, or paying a premium for items.”

Mr Hall’s thoughts soon turned to bringing machining in-house; and while having a degree in engineering, he had never received any formal training in machining (although he had used some manual and CNC machines at various times during his career).
For advice, Mr Hall turned to friend and business acquaintance Phil Boffin of BMS Engineering, who had gone down the same route when starting his company.
Mr Hall said: “I had used Phil for some roll-cage tube work, so I knew he had invested in XYZ machines. He suggested going to an XYZ Open Day at Nuneaton, and I went with the intention of looking for a lathe.
However, after ‘having a play’ with a couple of machines, I placed an order there and then for an XYZ SLX 1630 ProTurn lathe and an XYZ 2-OP machining centre.”
Quick operator
The two machines from Burlescombe-based XYZ Machine Tools (
www.xyzmachinetools.com) were delivered to SiFab and installed at the end of November 2017.
Mr Hall went for his free training on a Friday; come the Monday morning, he was producing and shipping his first parts.
“The conversational aspect of the ProtoTrak control on both machines made producing these first parts easy. I make lots of one-off and prototype parts, and using the Traking facility on the SLX lathe means I can be confident that the first-off will be right; Traking allows me to verify a program by using an electronic hand-wheel to wind the lathe though a program step by step.

It is also easy to make amendments when customers change things; and having these machines means I don’t have to wait two weeks for a sub-contractor to make parts — and then be charged the earth for them.”
With space at SiFab being limited, it is handy that the machines are compact. Despite having a 400mm swing over the bed, a 54mm spindle bore and 760mm between centres, the SLX lathe has a footprint of just 2,080 x 1,000mm.
The 2-OP takes even less space, with a footprint of 760 x 1,220mm; and with its eight-position tool-changer, it also allows unmanned machining.
Mr Hall says: “Having these XYZ machines equates to cost and time saving for me, so those typical Friday afternoon rush orders can be dealt with straight away. Standard items for radiators and fuel tanks can be machined to order, and costs are reduced.
“For example, a simple threaded shaft that I use regularly was costing £14 from a sub-contractor — and I had to order batches of 20.
“With the SLX, I can probably machine the whole lot for what I was previously paying for just one; and with a tool-changer on the 2-OP, I can leave the machine running and do other things, maximising the use of my time.”
With regard to machine cost, Mr Hall took advantage of XYZ’s rental scheme, which requires an initial payment at the outset of the agreement.
Then, there are three options every 12 months: return the machine; buy it outright at a pre-agreed price; or extend the rental period for another year with a further single payment (these subsequent rentals are based on a reducing percentage of the original machine cost).
At the end of the fourth year, the machine can be purchased outright with a final payment or returned to XYZ.
Mr Hall says: “The rental scheme is perfect for me. With the addition of a service plan, I know exactly what my costs are going to be — and I know I will still have a valuable asset at the end of the rental period.”