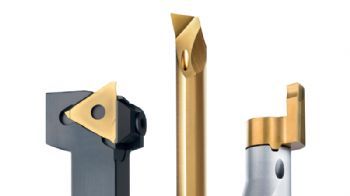
Ringwood-based Horn Cutting Tools Ltd (
www.phorn.co.uk) was showing a number of new developments, including new coatings — EG3 and EG5 — for its Supermini product series for machining holes from 0.2mm in diameter.
In comparison to previous coatings, they can double tool life, depending on the material being machined.
Meanwhile, Horn’s milling tools based on Boehlerit products have been expanded to include the ETAtec 45P face-milling cutter and the ZETAtec 90N roughing mill.
ETAtec 45P cutters, with diameters of 50-160mm, are equipped with between five and 10 seven-edged inserts. The tools not only offer a 45deg angle of attack and positive geometry but also generate low cutting forces, ensuring smooth machining coupled with high levels of productivity.
ZETAtec 90N cutters with diameters from 50 to 160mm feature five to 10 inserts, each with six cutting edges. The high reliability they achieve during roughing is due to their negative geometry, while the positive rake angle ensures a smooth cut.
The milling cutters can be used for helical or linear plunging, despite the negative geometry.
Horn’s new DPP range of solid-carbide drills from 4.0 to 18.0mm in diameter is available in two geometry variants. DDP tools for 3xD, 5xD and 8xD hole depths have been designed for a universal range of applications.
The materials they are most suited to cutting are unalloyed, cast and alloyed steels, and all tools feature internal cooling (a variant without internal coolant delivery is also available).
Solid-carbide drills with a conical ground surface for machining from 5xD are designed with double lands. The DDM geometry variant with four ground facets is intended for machining stainless and acid-resistant steels, titanium alloys and nickel alloys.
These drills feature internal cooling and are available for hole depths of 3xD and 5xD.
A particular highlight on the Horn stand was the company’s new skiving-tool range for use by modern machining centres and universal turn-mill centres with synchronised spindles and the process-optimised software necessitated by this complex technology.
The range consists of tools for manufacturing internal gear teeth, splines and other internal profiles as well as external gear teeth.
In these applications, the key advantages that skiving offers are: the ability to use the technique on suitable turning and milling centres; turning and gear cutting in a single set-up; and the absence of undercuts at the end of the teeth.
Moreover, the process is generally more productive and cost-effective than gear shaping and broaching — with cycle times up to five-times shorter than broaching.
Skiving tools are designed for gear cutting in medium to large batches, with each tool individually adapted to the application and to the material being machined.
Horn’s range comprises cylindrical or conical solid-carbide tools for modules from 0.5mm to 2mm and with diameters up to 20mm.
Moreover, the company’s exchangeable-head system means that the cutting head can be easily replaced in the machine, without the need to remove the solid-carbide holder.