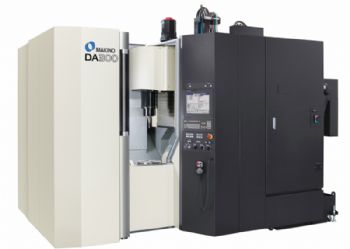
Visitors to
MACH 2018 learned that it is possible to achieve world-leading accuracy when cutting and skiving external and internal gears and splines on standard Okuma five-axis multi-tasking lathes and five-axis machining centres, thanks to their high levels of accuracy and repeatability combined with robust construction.
Okuma agent NCMT Ltd, Thames Ditton (
www.ncmt.co.uk), believes that it is at the forefront of gear production on a multi-tasking turn-mill platform, and it demonstrated power skiving on a Multus U3000 2SW with opposed spindle and 1.5m between centres.
The process is intended for producing gears from solid billets in large volumes to high accuracy using a dedicated skiving tool to sequentially rough and finish each type and size of gear.
Even with deep tooth profiles, a Class 6 spur gear can be achieved due to accurate synchronisation of tool and workpiece rotations.
Managing director Dave Burley said that the key to accurate gear skiving on this type of machine is the precise synchronisation of the two spindles — one for the tool and the other for the workpiece — and this requires an extremely rigid structure.
“The process can produce a wide variety of gear types, including helical gears and straight gears, as well as splines.
“It is particularly applicable to complex parts with gear forms — such as found in aerospace applications — where the single-set-up operation allows extremely high levels of accuracy to be achieved.
“The process is also extremely fast, with some smaller gears taking just a few tens of seconds to complete.”
Speed was also a feature of the new Makino DA300 five-axis trunnion-type vertical-spindle machining centre, which made its UK debut at the show.
The machine being demonstrated also featured a Cellro robotic system (from Holland) for automatically loading and unloading components.
The machine features: integral direct-drive motors for the swivelling (+30 to -120deg) A-axis trunnion and also for C-axis rotation of the 340 x 300mm table; a 20,000rev/ min 22kW HSK-A63 spindle; and a 60-tool magazine.
“Moreover, Makino offers two standard workpiece pallet systems that can be factory-fitted or retrofitted: a seven-pallet arrangement (expandable in the field), or a 19-pallet configuration.
The Fanuc-based Professional 6 CNC system with optional Super Geometric Intelligence 5 (SGI.5) provides streamlined screen layouts, operator assistance and new macros for maximised productivity.
For example, a G-code drilling cycle enables the tool to arc from hole to hole instead of following a square path, reducing non-cutting time by as much as 15% when drilling a typical hole pattern.
A vision sensor outside the machine’s work zone detects broken tools to ensure cutter integrity.
Other intelligent machine functions include Inertia Active Control — a weight-sensing capability designed to speed machine motions, based on ‘dynamic attributes’ — and Collision Safe Guard — a real-time crash-avoidance feature that has a look-ahead function and takes real machining conditions into consideration.
Other standard features include temperature control by cooling of the machine structure, spindle, ballscrews, bearings and drives.