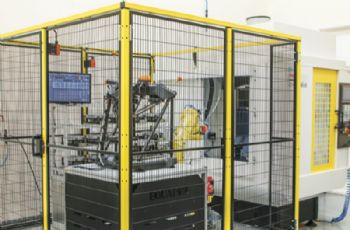
On its stand, the global engineering-technologies company Renishaw (
www.renishaw.com) featured a high-productivity machining cell that incorporated integrated process control to demonstrate how high levels of automation and connectivity can be incorporated into CNC machining operations to improve productivity levels and process capability.
Renishaw says its own structured approach to identifying and controlling sources of process variation — before, during and after machining — results in consistent, automated and productive metal cutting.
From preventative machine maintenance and automated tool and part setting through to in-process measurements and off-machine gauging for direct process control and verification, Renishaw technologies enable fully automated end-to-end machining processes controlled at the point of manufacture, with zero manual intervention.
The cell on display at
MACH replicated the closed-loop process control applications that Renishaw uses to machine parts in its own production facilities in the UK, where integrated application of the company’s technologies
enables highly productive, automated manufacturing with reduced labour and skill requirements — despite the low-volume high-variety manufacturing environment.
Indeed, Renishaw says that by integrating layers of precision measurement and automated inspection technology into the production processes, the company’s Miskin plant in South Wales demonstrates an approach to future smart factory concepts that can be achieved today with current technology.
Chris Pockett, head of communications at Renishaw, said: “As Industry 4.0 and the current shortage of skilled engineers demand that businesses increase productivity without increasing their workforce, manufacturers are turning to industrial automation and intelligent processes to reduce skill and labour requirements in CNC production.
Renishaw has extensive expertise in working closely with its customers to successfully introduce automated process control solutions into manufacturing operations, with a global network of experienced applications engineers providing technical support and partnerships for innovative manufacturing.”
Other highlights on Renishaw’s stand included the company’s latest scanning system for CNC machine tools, ‘intelligent’ process control software for the Equator gauge and apps to simplify machine tool probing.
The company also showed a non-contact tool setter for machining centres, a multi-probe optical interface system, enhanced software for its XM-60 multi-axis calibration system, and a new surface finish probe for use on the REVO five-axis measurement system on co-ordinate measuring machines (the SFP2 probe is interchangeable with other REVO probe options and offers the ability to fully integrate surface measurement and dimensional inspection on a single CMM).
Also new was Renishaw’s Equator 500 system, which enables the gauging of larger parts. Both Equator 300 and 500 systems, which are accurate between 5ºC and 50ºC at any rate of temperature change, are capable of scanning speeds in excess of 200mm/sec.
Moreover, every system is compatible with simple-to-use Organiser operator software, EZ-IO software for automation, and IPC (intelligent process control) software for updating tool offsets on CNC machine tools.
The Equator 500 has a gauging volume of 500mm diameter in the X-Y plane and 250mm in Z when used with the SM25-2 scanning module; this can be expanded to 400mm in Z with the SM25-3 scanning module, which allows styli up to 200mm long to reach many more features.
The Equator 500 accommodates workpiece and fixturing with a total weight limit of 100kg.
Furthermore, the new Equator Automatic Transfer Systems for Equator 300 and Equator 500 allow parts to be loaded onto a fixture plate in front of the gauge, and transferred in and out of the measuring volume under automatic program control.
They can be used for either manual loading — by operators, cranes or fork-lifts — or robot loading in an automated cell.