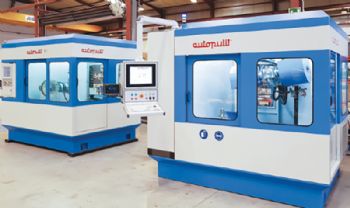
#MACH2018 Christchurch-based Ellesco Ltd (
www.ellesco.co.uk) showed how it can help customers meet their finishing needs by demonstrating an Autopulit CNC polishing cell and a KBM long-belt grinding machine for weld dressing.
KBM machines are designed to undertake many different weld-dressing processes, including: ‘preparation and removal’, blending and shaping of seam welds, and smoothing spot and puddle welds — particularly on sheet metal fabrications, profiles and small housings.
In their basic configuration, the machines feature a flat machine table with a ‘twin offset’ that can be adjusted for height via a chain-and-gear motorised system; they offer a variable belt speed and belt widths of 100 or 150mm.
A higher-specification machine with a three-axis table and an integrated handling mechanism makes holding, rotating and pivoting work-pieces much easier.
Components are secured by vacuum suction cups, while the handling system allows the workpiece to be positioned relative to the grinding belt in three planes.
KBM machines can be supplied in a range of sizes to handle workpieces up to 4,000mm long and 1,500mm wide.
The Autopulit CNC polishing cell shown by Ellesco was a five-axis unit featuring a ‘flexible working head’ for satin finishing and ‘gloss polishing’; this head can be equipped with rotary abrasive brushes and mops to suit specific
applications.
Under full CNC operation, the brushes/mops (and appropriate abrasive con-sumable) are fed over the workpiece at pre-set speeds and pressures to deliver either a polished, ground or satin finish — and with appropriate brushes, the machine can also be used for deburring.
Application areas are varied — from aerospace and automotive to household goods and appliances.
Ellesco managing director Vincent Simonis said: “The weld-dressing and polishing aspects of Ellesco’s business are another example of how we have developed relationships with suppliers to deliver the ideal solution to our customers, whether it’s deburring, grinding or polishing.”
Ellesco was also showing three Timesaver machines, ranging from a 10-series manual grinder (a cost-effective alternative to conventional grinding and deburring) through to the 32-series 1100 WRB machine.
This features an 1,100mm-wide working area and a combination of belt and multi-disc or rotary-brush abrasive material.
Timesavers’ quick-exchange slide and easy-lock disc system means that brushes and grinding media can be changed quickly and easily (a wide range of rotary brush types is available).
The use of multiple heads and media also allows the removal of heavy burrs and optimum surface finishing to be completed in a single pass through the machine.