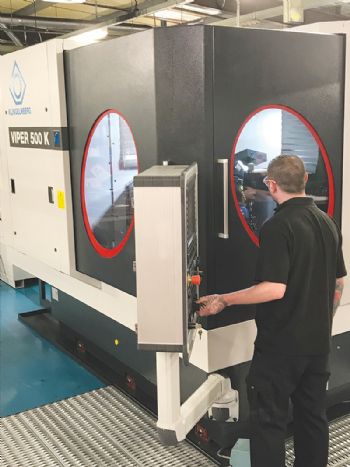
Precision Technologies International Ltd recently installed the latest-specification Klingelnberg Höfler CNC external/ internal gear-grinding machine at its Tamworth headquarters.
In addition to expanding the company’s gear-grinding capacity, the Viper 500K has enabled it to produce the most complex gear geometries to the highest of standards.
Formed in the 1960s, Precision Technologies started as a tool maker with customers in the West Midlands automotive market.
In 1987, the company added master-gear and spline-gauge production, followed by a fully accredited UKAS laboratory in 1990.
In the early 1990s, it entered the aerospace market, and soon after that, it was contacted by a UK-based Formula One engine manufacturer and asked to produce high-precision timing gears.
Acquired by the current management team in 2015, the business is now a major supplier to F1 and several other motor-sport classes — plus a variety of other industrial sectors.
Significant increases in output and the imminent prospect of two major automotive gear-manufacturing contracts recently prompted Precision Technologies to look for additional CNC gear-grinding capacity.
Technical sales director Colin Palin said: “In order to expand our capacity to meet both current and anticipated demand, we investigated the available high-end external/internal gear- and spline-grinding machines, finally selecting the Klingelnberg Höfler Viper 500K.”
Invaluable help
Mr Palin also said that the help of Mark Maurice, the owner of the grinding-machine manufacturer’s UK agent — Mold-based Micronz (
www.micronz.co.uk) — was invaluable when specifying the machine and ensuring trouble-free installation and operator training.
“Thanks to the Viper 500K’s logical operating system, our staff quickly became skilled in using the machine, which is now producing the required high quantities of premium-quality ground gears, which feature complex geometries and are used in automotive and motor-sport sectors, as well as other equally challenging application areas.”
The Viper 500K, as purchased by Precision Technologies, accommodates component diameters up to 500mm; and because the machine features multiple-wheel technology, it is suitable for the efficient production of small to medium-size batches.
Moreover, its configuration allows users to change the grinding technology by quickly ‘swapping out’ the grinding wheel, the grinding-wheel flank and the dressing wheel for the optional internal gear-grinding arm, which allows re-tooling and conversion from external to internal work.
Furthermore, the arrangement of the Viper 500K’s axes allows optimised five-axis grinding in the shortest-possible time.
This is a major contributing factor in the machine’s flexibility and its ability to consistently produce high-precision high-quality work. The machine has also been designed to minimise energy consumption — and to be easily cleaned.
Meanwhile, Klingelnberg Höfler’s Gear-Pro operating software has been configured to ensure the convenient machining of even the most complex gear profiles, while ensuring maximum manufacturing efficiency via the use of advanced machining strategies and process sequences.
Convenient software modules for best-fit high-speed adaptive grinding are also available, as is a module that allows highly efficient wheel dressing.
Other facilities offered by the software include Job Engineering/Pre-analysis, which allows exact process-time calculations to be made using original machine data.
In addition, 3-D analysis of the planned process steps (relating to working range and possible interference contours) is provided, as is predictive tool-wear analysis.
Furthermore, the easy-to-use software offers geometric production simulation, with 3-D analysis of the simulated flank topography, along with the calculation and export of optimised tool profiles; it also offers simple navigation via clearly structured interface areas and well-organised Windows-like data management.
Data input is via an intuitive and clear graphical display, while easy-to-understand operator guidance is provided by means of an automatically generated list of process steps; and thanks to a number of ‘context-sensitive’ programming ‘wizards’, including those for a range of tried-and-tested process variants, the software allows the trouble-free input of even the most complex of flank topographies and profile forms.