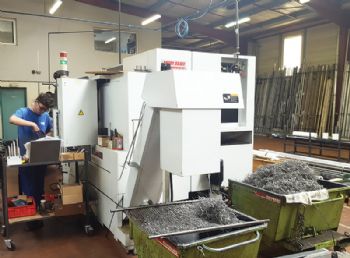
Based in Pinsaguel (near Toulouse), Société Toulousaine d’Etude et d’Usinage (STDU) manufactures complex components with tight tolerances (down to 0.01mm) for a variety of industry sectors, including agriculture, medical, aeronautics and gas.
Cyril Gloriant — formerly technical director but recently appointed as CEO — says the company needs a perfect working combination of operator, machine tool and software, adding that around 80% of its components are machined with Edgecam (
www.edgecam.com) driving CNC lathes and mill-turn machining centres from the likes of Mori Seiki, Haas, Manurhin and Hardinge.
He said: “It is important for Edgecam to be able to pilot all our machines; we cannot accept a two-tier production system.
"As all the necessary machining information is contained within the post-processors, all our operators can use this software; and if for some reason we need to move a job from one machine to another, production can be switched rapidly with the same kinematic characteristics and a different post-processor.”
STDU installed Edgecam in 2017 and progressed to using it daily in the workshop early this year.
Mr Gloriant says the company’s 10 employees currently use Edgecam’s milling and turning modules, along with machining strategies that include Waveform turning and milling, and find the software’s feature-recognition capability particularly valuable.
“With a single mouse click, Edgecam analyses the part and determines the operations that need to be carried out; it also recognises ‘function properties’ such as depth, minimum radius and angles, then prepares machining sequences that can easily be modified according to our specific requirements. Machining runs smoothly every time.”
He says reduced programming and cycle times, along with acquiring new skills and knowledge from Edgecam, have opened up new markets for STDU in both serial production and the machining of more-complex parts.
“Because customers know we can now produce parts that previously we didn’t have the skills or capacity for, they are designing more-innovative components, and we’ve risen to the challenge every time.
“Moreover, we are saving up to 3hr by programming the machines off-line, while they are running other jobs.
“When we receive the CAD model from our customer, we determine which production method we will use — either turning or milling — along with the appropriate machine tool.
We then open the 3-D CAD model in Edgecam and run the feature recognition module, which analyses the part and prepares the machining sequence. We also use Edgecam to help establish a quote, as it provides accurate timings.”
STDU soon took CNC programming to the next step, training its operators to use Edgecam’s Strategy Manager feature-based automated machining system, which can reduce certain aspects of repeat programming to mere seconds “using pre-defined functions based on part topology to save us even more time on preparation, programming and machining cycle time.”
In conclusion, Mr Gloriant said that while STDU originally invested in Edgecam so that it could work directly on customers’ 3-D files without the need to redraw plans, while easily configuring the software for its own requirements and creating macros, it quickly realised that time and money could be saved throughout the whole manufacturing process.
“For example, by applying the Waveform turning strategy, we have reduced machining time by up to 30% on some parts — and up to 40% when milling in association with ‘rest material’ machining.”
Merging programs
Meanwhile, 15-employee Burnley-based mould maker Kavia Tooling has developed machining strategies that allow it to run multiple CNC programs at once by merging several of them into a single file — many containing around 1.5-million lines of code.
It produces some 80 mould tools a year (for plastic injection moulders), ranging in size from 156 x 156mm to some weighing up to 2 tonnes.
Kavia uses Edgecam to drive a number of high-speed CNC mills (with spindle speeds varying from 12,000 to 30,000rev/min), and Sodick EDM machines.
Production director Mark Cole says: “Edgecam customised the software for us to create a system that we call Merge. It means we can put several components on the machines at once, and the Edgecam CNC code for them all is merged into one large program, along with the datums to set the parts on.”
He recounts an example of working on two cavity plates on one side of the machine and four inserts on the other. “We put the individual Edgecam CNC programs for each component together into one file, and sent it to the machine as one large program.
"This software also keeps the number of cutting tools to a minimum, by looking at information such as duplication, length and quality of the tools in all the programs.
"For example, if there were two repeating cuttings tools in the individually merged programs, it selects the best one for the manufacturing process. It goes through every single NC program and re-arranges all the tools accordingly.
“If we have 10 components that can all fit on the machine, Merge puts the tool information for all 10 programs together, along with the datum-setting information, part-setting information and pre-setting data — everything in fact. As far as the machining is concerned, it’s just one big product.
"The customised software works for us exactly how we want it to, and everyone from the CAM programmer to an apprentice setting the tools works in the same way. It demystifies shopfloor activities and eliminates error.”
Meanwhile, Kavia’s use of Zero Transfer Fixture Plates, which can be mounted on a machine table with micron accuracy, allows the company to load components offline and establish the X, Y, Z and U orientation using a Hexagon co-ordinate measuring machine and special software written by the CMM company.
This can be done with any number of components, and the information is transferred to the machine through the Edgecam Merge software, which uses the data to add a programmed work offset and co-ordinate rotation into the appropriate merged programs.
Mr Cole said: “We only have to put the Zero Transfer Plate into position on the machine; and because it now knows exactly where the part is on the plate, we don’t have to set it.
“The end result is a CNC program that can machine several parts at a time, without needing to use the machine as a set-up station, as all preparatory operations are now carried out off-line.”
“Edgecam engineers also worked with Kavia so that the software can capture all the required tool information from the tool-maker’s Zoller tool pre-setter and merge it all into the final CNC file.
“What used to be a skilled job can now be done by a first-year apprentice. Edgecam is now absolutely integral to our entire manufacturing process.”