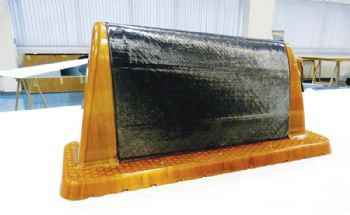
At the recent
JEC World (the international composites show), Stratasys (
www.stratasys.com) showed how IDEC — a leading Spanish provider of composite solutions for aerospace — has cut the time, cost and material waste involved with traditional composite moulding, thanks to its use of Stratasys additive manufacturing.
In a government-funded project, IDEC explored the capabilities of Resin Transfer Moulding (RTM) technology, based on the testing of a new composite material and its moulding process for the manufacture of a curved aircraft wing.
With the support of advanced prototyping service provider Wehl & Partner, IDEC overcame a challenging requirement
to replace aluminium in a tooling application with a non-conductive material resistant to high temperatures and pressures.
Using its Stratasys F900 Production System, Wehl & Partner selected the ULTEM 1010 resin to manufacture a large-scale preform tool. The material’s chemical- and heat-resistance enabled it to withstand the required temperatures (exceeding 150°C), as well as high pressures.
Diego Calderón, structural analysis manager at IDEC, said: “Stratasys additive manufacturing enabled us to produce the preform tool in just 60hr.
"With CNC machining, it would have taken at least four weeks to produce this type of part. In addition to slashing the production lead-time on the preform tool, we also expedited the whole composite moulding process; with ULTEM 1010 resin, we reduced the composite heating stage from one hour to only 10min by flowing the electric current directly through composite fabrics.”
Preform tools are typically made of aluminium or epoxy resin, and the composite fibre is laid up on top and the tool, which is subsequently heated.
The challenge in this instance was that, instead of heating the preform tool, this particular application required the composite material itself to be heated using an electric current sent through the composite fibre.
Consequently, highly conductive metals like aluminium were inappropriate for the tool, as they would prevent the current from effectively going through the fabric; and standard epoxy materials available inside the company were neither resistant nor stable enough to withstand temperatures exceeding 140°C.
“Although there are epoxy resins resistant to such high temperatures, these are very expensive and would not have been financially viable. ULTEM 1010 resulted in a preform tool with perfect mechanical properties.”