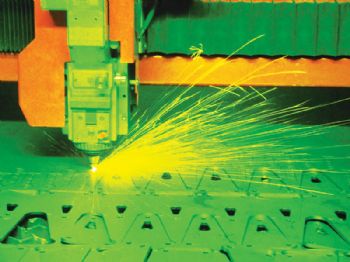
Nottinghamshire-based Lasershape Ltd, a sheet metal sub-contractor, recently switched over to Radan software (
www.radan.com) to drive its four laser and two water-jet cutting machines, after an intensive three month period of development, trials, tests and training — and it is expecting a return on its investment in less than two and a half months.
The company manufactures components primarily for the general engineering, aerospace, rail and automotive industries — its core products are laser-cut, folded and powder-coated, with some assembly where required, and include parts for almost every industry sector.
Jason George, Lasershape’s IT and facilities manager, has been implementing a series of measures over the last two years aimed at driving down costs; he felt that the company’s CAD/CAM package was falling behind in terms of efficiency.
He said: “The system was very manual, and although we had a project with our supplier, who was trying to automate it, we simply couldn’t rely on the results it was producing, so we had to have an operator watching over it, which defeated the object.”
Lasershape made the decision to replace it with Radan, and found in numerous trials that this led to considerable savings.
Mr George said: “We use around £400,000 worth of material a month, and our scrap rate was around 20-30% with the previous CAD/CAM package.
“We compared a trial we ran through Radan with what our production team had actually sent to the shopfloor after making manual changes to improve the nest from the previous system, and it still reduced wastage by about 15%.”
Poor sequencing was identified by Mr George as the biggest single cause of scrapped parts under the old system, which was not performing to the high standard that the company required.
“With the large number of parts we produce, it’s impossible to go through each nest and manually select the cutting sequence — we have to rely on automation.
“We ran the same job through Radan, and it was much better at getting out of areas without crashing the head.
“Radan’s not just about speeding our processes up, it’s all about accuracy, both in terms of the cutting sequence and the finished component.
“Another test involved a production job of 400-plus runs of 3mm aluminium parts in Radan.
“This particular job had ‘head collision’ written all over it, but with Radan each sheet was cut 52min quicker than the old system — and with no collisions.

“When I looked at the code, I saw this was because Radan was able to cut at full speed, while the other software applied slower cutting conditions for small features. This could save us considerable time.”
An optimised Radan nest in one of Lasershape’s early trials saved over 5hr compared with the previous nests, which he says represents shaving 1min off each part.
Having built a number of apps around Radan to meet its bespoke requirements, Lasershape benefits from two-way communication between CAD/CAM and its Epicor production control software.
Mr George said: “We’ve customised the main menus inside Radan and linked them to our own Lasershape menus.
“This is helpful right from when we receive an initial inquiry, in that we can see at a glance how many sheets we’ll need for the job, and significant benefits stem from our new work-flow system.
“It controls stock, live updates of programs, and remnant creation inside Radan. All this gives us an up-to-the-minute overview of what’s happening on the shopfloor.”
Powerful functionality
Mr George has also created a ‘part editor’ application to mass-edit components. He said: “It automates Radan’s powerful functionality to work on multiple parts at the same time, so we can mass-import DXF files and edit the data quickly.
“This is particularly important, as we work on around 20,000 live items every month and have nearly 200,000 repeat parts in the system.”
The first task when an inquiry comes in is to add a quote in Epicor. “We’ve got a button that says ‘prepare Radan’. This generates a quotation folder for us, a standard project template ready for the nester to nest in, and sub-directories for the parts.
“We’re then ready to start drawing the part in Radan 2D. The parts are imported and saved in the ‘quote directory’, which means quoted parts don’t touch our ‘master part library’.

“With the previous CAD/CAM system, we had a bulging part library containing parts for jobs we didn’t win and never cut, so this is a huge improvement.”
After that, Lasershape uses the part editor app to set customers, materials and machining operations, including any required countersinking and folding.
This is followed by another customised operation, running ‘the migrator’, which scans the entire project, then calculates how long each part is going to take and the exact percentage of a sheet it will use.
Mr George said: “Migrator then populates all the relevant fields in Epicor. When we win the job, it’s converted to an order, and Epicor tells Radan which customer the parts are for, creating directories for the project.”
The nesting team uses work-flow to specify the parts for nesting and send them to Radan.
“It’s so simple to pull in the raw-material sheets, nest them, post them, and send them out for cutting on our Trumpf and Bystronic lasers, or Flow and Techni water-jets.”
Mr George says it’s vital that Radan drives both cutting technologies and can work with a variety of CNC machine tool brands.
“With Radan, we just have the one part library that serves all our machines; we couldn’t have multiple part libraries for the same components.”
Mr George sconcluded that Radan has reduced the task of producing nests to what he calls “a simple admin role”, as the system automatically creates efficient cost-saving nests.
“As everything we do now is about efficiency and data capture, Radan is a key part of the business.”