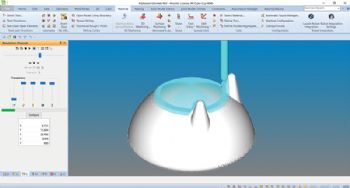
Worcestershire-based Jointmedica Ltd, which produces Class 3 implants for the orthopaedic sector, has in its product portfolio an innovative ‘mobile bearing’ knee replacement.
The development activities being undertaken in-house at Jointmedica’s facility in Hallow, use Alphacam computer-aided machining software from Cobham-based Hexagon Manufacturing Intelligence (
www.HexagonMI.com).
This software allows the design team to explore innovative new designs and incorporate new materials “to help drive the advancement of orthopaedic hip and knee replacement surgery to the highest levels of quality”.
Technical director Roger Ashton said: “If we consider the hip resurfacing market in isolation, several years after the procedure began, a small number of patients suffered physiological problems due to hypersensitivity to various metals; the resulting small number of bearing-related failures saw a sharp decline in the use of metal-on-metal articulations for resurfacing.
“It is the role of Jointmedica to work with alternative bearing materials and use the successful resurfacing method to make a product that will re-establish the hip resurfacing market.
“We are fortunate to be associated with the most experienced hip resurfacing designers and surgical innovators in the world.”
In-house R&D
When the company brought its manufacturing R&D in-house, the need to buy a suitable machine and CAD/CAM software became apparent.

Mr Ashton said: “It was clear that we would be undertaking an interesting combination of turning 2-D profiles and surface machining that would involve milling, drilling and slotting; we also knew that we would be dealing with a lot of complex geometries.
“We needed a CNC machine tool and software that could manage all of our milling and turning requirements, sometimes using more than three axes.
“A Brother Speedio M140X2 full five-axis CNC machining centre fitted the bill perfectly.
“Many products require a combination of three-axis and four-axis machining, plus turning operations, so Alphacam will always be an integral part of our manufacturing processes.”
Manufacturing custom implants at Joint-medica begins the moment the company receives a patient’s CT scan, which allows the company to start modelling the bespoke product.
It uses two CAD systems to design the solid models (mainly Creo, but occasionally SolidWorks), based on files usually sent as an XT file, STEP file or as a DXF file.
Alphacam Ultimate Mill and Standard Lathe are used to machine the finished product, as the Brother machine can undertake both turning and milling.

Oliver Clayton, a manufacturing engineer at Jointmedica, said: “I take Alphacam’s 3+2 system and incorporate it into some of the ‘bespoke custom devices’ available, following this with three-axis milling and turning cutter path definition for a simple axisymmetric product.
“In the turning program, I mainly use the CAD functions to draw the geometry and apply the tool-path; this approach is extremely useful because I can incorporate not only the model but also draw my own tool-paths to suit the geometry.”
Material specification
The materials for a ball and socket type of bearing that work well when implanted in the body as a hip replacement, can include ultra-high-molecular-weight polyethylene of differing formulas, along with a ‘counter face’ of cobalt chrome or ceramic — and other materials.
Mr Clayton said: “Through accurate machining, driven by Alphacam, material wastage is kept to a minimum — and we can ensure the final, bespoke product is suitable for the patient.
“Parts we make must be dimensionally correct, and Alphacam is ensuring that we get the right results every time, as confirmed by the measurements we take with our co-ordinate measuring machine (CMM).
“With our prototyping, we are comfortably achieving the industry-expected tolerances — and a bearing surface finish of 0.8Ra for one-offs.

“We know that future production capability will significantly exceed these figures, and we are confident in the machining results provided by the Brother machine driven by Alphacam.”
A particular challenge facing Jointmedica in the manufacturing process was manipulating the tool-path to get the shortest machining time for a particular part.
However, Mr Clayton says the software’s ability to define the best cutting tools and tool-paths allow these to be manipulated to set the shortest time with the best path for the device to be manufactured accurately.
“When I refer to accuracy, I don’t just mean the speed and accuracy of a geometric tool-path I put over a CAD model that has been imported into Alphacam; I mean combining a number of different operations and relying on the accuracy and ease-of-use of Alphacam to pick up at a point that I have designated and applying an alternative machining strategy.
“Alphacam always picks up accurately — as verified by our CMM.”