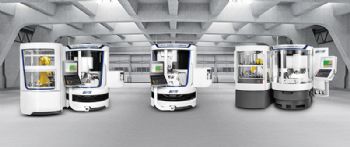
It would seem that the world market for PCD tooling is certain to grow, particularly as the use of carbon fibre and carbon-aluminium ‘stacks’ is increasing in the aerospace and automotive sectors, so having a single machine that can both erode PCD tools and grind carbide tooling — even in the same set-up (a tool’s carbide body and its brazed-on PCD tip) — would eliminate two separate set-ups on different machines.
This logic has ‘spurred’ the machine tool and tooling specialist Walter (
www.walter-machines.com) to develop a ‘two-in-one’ machining concept around its multi-axis Helitronic Diamond machines.
These currently comprise the Vision Diamond 400 L (for tools from 3 to 420mm long), the Power Diamond 400 (for tools from 3 to 380mm in diameter and up to 520mm long) and the Diamond Evolution (for tools from 1 to 165mm in diameter and up to 255mm long).
While the time and money rewards of eliminating separate set-ups for grinding and erosion are undoubtedly attractive to existing tool manufacturers and regrinding companies processing carbide/PCD tooling, Warwick-based Walter Ewag UK Ltd — a member of the United Grinding Group — points out another major benefit of the two-in-one Diamond concept for firms that may be considering entering the PCD market.
Neil Whittingham, the company’s sales director, said: “The fact that the machine user can perform both eroding and grinding — or combinations of the two — means that investing in a Helitronic Diamond is effectively a risk-free introduction to the PCD market.
“If it happens that the PCD business does not develop as expected for that company, the machine can simply revert to being a cost-effective way to grind carbide and HSS tools.”
Walter says that the compact Helitronic Diamond Evolution (occupying just 4.2m
2 of floor space) is the ideal entry-level machine for producing and regrinding PCD tools with diameters up to 165mm and lengths up to 185mm — a size range that Mr Whittingham says accounts for some 90% of PCD tooling consumption world-wide.
Moreover, he says the machine can grind and erode a wide range of carbide and PCD styles, including: shank, profile, circular and roll mills; multi-step tools and countersinks; and tools for cutting and profile-cutting plates.
He also says that Walter’s PCD-tool-programming routines include “the erosion of PCD on tool diameters and the production of K-Land, variable spiral and ball-nose gash”.
Unmanned operation
In addition to a robot loader that can boost unmanned operation by automatically handling up to 72 HSK tools or 7,500 cylindrical tools (depending on their diameter), the machine also features an HSK spindle.

“This is shorter than an NCT spindle, and it offers high levels of stability and electrode surface quality during dressing, as well as longer life for the dressing insert.
“The machine is also equipped as standard with Diamond Plus software; in addition to simplifying and speeding up the programming of complex PCD forms, it also enables production times to be reduced by up to 40% and cutting-edge quality to be improved — with edge chipping down to just 5µm at 10µm grain size.”
Mr Whittingham adds that Diamond Plus is just one of the technologies that Walter has developed to continually make the tool erosion process on its Helitronic Diamond machines more efficient and cost-effective.
“For example, the Helitronic Tool Studio software now includes erosion functions for the fast and easy programming of ‘what you see you can grind and erode’.
“In addition to fast 3-D live simulation routines, this software also allows the design and programming of complex tool geometries, including individual tooth geometries and tool parameter scaling.
“Software routines also enable automatic electrode/grinding-wheel changing and robot loading for high levels of automation/unmanned operation.
“Supplied as standard is a four-station grinding-wheel/electrode changer, with an eight-station unit available as an option — plus there are a number of robot loading solutions available.
High standards
“Meanwhile, improvements to the machines’ generator, as well as the erosion software, mean that Walter’s Fine Pulse Technology routines offer high standards in terms of PCD tool surface and cutting-edge quality, as well as process reliability.
“Indeed, on Diamond machines, the surface finish is like that of a ground tool — and even coarse-grained PCDs can be fine-finished with ‘perfect surface qualities’.
“Furthermore, subsequent steps in production can be eliminated, because no re-sharpening or polishing is required.”