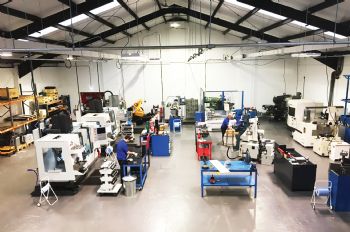
Precision engineering firm JJ Churchill (
www.jjchurchill.com) has announced that it has increased six-fold the space allocated to its tool-room division.
The factory in Market Bosworth has a range of ‘state of the art’ and traditional equipment to design and produce some of the most complex fixtures to a high degree of accuracy.
This is needed to ensure the subsequent precision manufacture of specialist engineered components.
JJ Churchill recently acquired a 3-D printer, enabling it to cut prototype design and production from weeks to hours.
Its other capabilities include CNC mills, lathes and wire-erosion EDM.
As well as milling and turning, it also puts each jig through a co-ordinate measuring machine to control quality; there is also automated part marking.
A lot of space is now being devoted to the production of aerospace components, including those covered by the £70 million contract with Rolls-Royce announced at last year’s
Farnborough Airshow.
Design engineer Matthew Smith said: “The most technically challenging problems in machining can be found in the design and production of fixtures for complex aerospace parts.
“That is what we do at JJ Churchill; we focus on ‘sticky niches’ — problems where the first reaction is ‘that can’t be done’.
“We are continuously ramping up to meet the needs of our growing business.”