PCD milling cutter (pictured left), alongside a Zirconium oxide milling cutterChris Boraston, the managing director of Coventry-based
Advanced Grinding Solutions Ltd, which represents manufacturers of a broad range of grinding machines, finishing machines and associated equipment — including tool manufacturing machines from Switzerland-based
Rollomatic — says that while there is a continual development of new machines, and very occasionally new processes, “it is not that often that you come across something that is so far ahead of anything else and operates on such a high technical level that one can only marvel at how amazing the engineering development is.
“Rollomatic’s LaserSmart 510 Femto Laser machine represents one of these rare occasions with a machine that takes the incredibly high levels of machining quality achieved by the company’s current laser machines yet another step further.
“Engineers are used to fighting seconds, especially when it comes to reducing cycle times; and over the years, Advanced Grinding Solutions has been tasked with achieving cycle time savings where every second counts. However, understanding exactly how Rollomatic’s latest laser machine for manufacturing PCD and other very special tooling works, introduces a need to understand time on a somewhat different level.
“To put this in perspective, femtosecond lasers are ones that emit light pulses with durations between a few femtoseconds and hundreds of femtoseconds, where a femtosecond is a unit of time (in the International System of Units) equal to 10⁻¹⁵ or one millionth of one billionth, of a second. One picosecond contains 1,000 femtoseconds, and there are 1,000 picoseconds in one nanosecond — which itself is one billionth of a second. All unbelievably short periods of time short, but the capabilities of Rollomatic’s LaserSmart 510 Femto Laser machine really is based on femtosecond technology.”
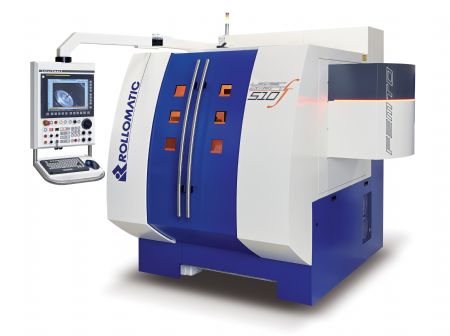
He continued: “Since Rollomatic first launched its LaserSmart machines, showing the first one a decade ago at the IMTS exhibition in Chicago, these have been further developed by Rollomatic’s engineers to transform this new technology into a ‘world-leading class’ of extra special machine tools. Noting the development and use of short-pulse lasers — so called ‘cold source’ laser systems — for human eye surgery by the medical industry, the Rollomatic team took inspiration from this and investigated how the super-fast lasers could be used to further advance the manufacturing cutting tools and inserts, with the resulting Rollomatic 510 Femto Laser machine the pinnacle of that work.
“Moreover, the success of this machine — with its take up by major PCD, diamond and CBN cutting-tool manufacturers such as Paul Horn and DTS — has been such that these laser machines have their own dedicated production line within Rollomatic’s huge machine tool plant in Le Landeron, Switzerland.”
Mr Boraston says the fact that the Rollomatic 510 Femto Laser machine operates in femtoseconds brings about some major advantages when looking to manufacture PCD, ceramic, CVD diamond and PCBN cutting tools. “This is the world’s first femtosecond ultra-short-pulse laser cutting machine for ultra-hard materials, with 30% faster feed rates as compared to conventional laser machines and pulse widths 1,000-times faster than pico lasers.
“Moreover, the laser pulses on the Rollomatic Femto Laser machine are so short that zero heat is produced; the laser beam is simply not in direct contact with the cutting tools surface long enough for any heat to be generated. Even when working in picoseconds or nanoseconds tiny particles of dust are melted and temperature transfer issues can affect the surface structure of the cutting tool. So short are the femtosecond pulses on the Rollomatic machine that material is simply lasered away, micron by micron, being immediately vapourised and only gas produced.”
Rollomatic is understandably secretive about specifying typical machine settings, as the laser machining process has many parameters that influence the cutting result — including laser power, the wavelength, the frequency, the pulse length, and the machine tool axis speed. However, Rollomatic’s software ensures that all an operator need do is select the type of material to be machined to ensure that the optimum settings are automatically recalled, although there is a degree of freedom for these to be altered based on previous experience.
A choice of threeMr Boraston says Rollomatic’s three current laser machines are not only 450% faster than the previous-generation types but also some 500% faster than the conventional EDM processes that are most often used to machine PCD tooling. “Moreover, in addition to the huge cycle time savings the company’s ‘unique laser processes’ achieve razor-sharp cutting edges with a radius of under 0.5um, although users can freely define a desired edge condition with a 3, 6 or 9µm radius.
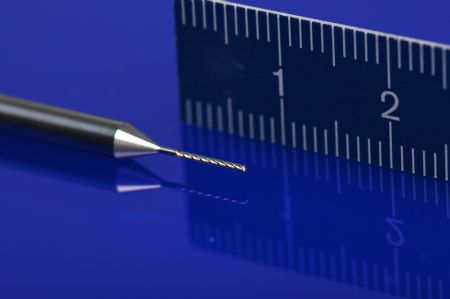
“PCD tools often require a perfect mirror-like surface finish, and here Rollomatic machines have achieved a surface finish of just 0.048um Ra on a primary relief of a profile insert in PCBN material; this super-mirror-like-finish is obtained with no detriment to cycle time — and the edge condition is fully maintained. Finishes to this level cannot be achieved by processes such as EDM or grinding.
“Furthermore, Rollomatic’s laser processes are now so fast that it now takes less time to ‘laser out’ flutes on certain micro tools like endmills and drills than conventional grinding. The laser machining of chip-breakers is fully catered for with quality ‘above industry standards’ — and cylindrical margins are machined in a single clamping. The programming of negative chamfers (K-lands) is also covered, as is the ability to fully define the cutting-edge radius on cutting tools.”
The three laser machines in Rollomatic’s line up comprise: the LaserSmart 510, the LaserSmart 510 Femto, and the LaserSmart 810 XL. The 510 versions have been developed for machining smaller tools whereas the 810 machine is used for producing larger PCD cutting tools as used by the woodworking, automotive and aerospace industries.
Mr Boraston added: “Apart from producing PCD tools, the machines are equally at home when machining ceramics, tungsten carbide, sapphire, glass or other ultra-hard materials, with the machining process automatically adapted to suit the chosen material; and while coated tools offer a significantly longer tool life as compared with uncoated-carbide types, there is a drawback in that thicker coatings make the cutting edge dull awhile thinner coatings often wear prematurely.
“However, Rollomatic has developed a new process that allows laser machines to sharpen thicker-coated carbide tools. This involves probing the surface of the coated tool to detect its exact shape and position and then using the laser to remove just enough coating to make the cutting edge perfectly sharp. Field testing has shown that tool life is increased significantly as compared with conventional unlasered coated tools. These tools can also be a very cost-effective alternative to far more costly PCD tools.”
Machining capacityThe 510 machines can produce tools up to 190mm long and from 0.1 to 80mm in diameter. The larger 810 machines can produce tools up to 350mm long and up to 300mm in diameter — and weighing up to 15kg.
The latest 810 XL machine, which weighs some 7,500kg, can be equipped with up to seven cameras to ensure that every step of the lasering process can be monitored by the machine operator during actual production; it also benefits from ‘a new and patented’ sixth CNC axis for ‘smoother and faster’ sweeps of the laser beam. The automatic loading of cutting tools is standard and is done via an integrated pick-and-place loader with a capacity of 30 parts.
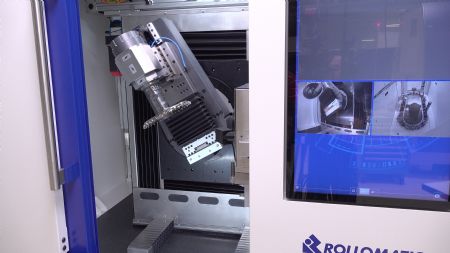
Mr Boraston added: “Although Rollomatic has developed lasers operating in the femtosecond range, the company also focused on other machine components to ensure that the performance of these machines remained far ahead of conventional machining. For example, the latest 810 machine not only uses a granite bed but also 3-D-printed-ceramic axis components that are some three-times-lighter and three-times more rigid than cast iron; and because a machine is often only as good as the software that allows for the manufacture of parts, Rollomatic has introduced another world-first — its new ‘Smart Programme Generator’, or SPG system.
“Here, a tool manufacturer only needs a DXF file and 3-D drawing of the tool he wishes to produce. This data can be immediately imported into Rollomatic’s SPG system; and once imported the operator need make as few as five selections to allow the software to create the entire machining programme for the tool to be produced. For example, the programming of a complex step tool/form cutter that used to take 1hr to program can now be programmed in just 2min.”
Clarifying the positioning of laser machines within Rollomatic’s range of machinery for producing cutting tools, Sven Peter — the company’s laser product manager — said: “Many sectors in industrial production rely on the use of diamond tooling, which in the form of CVD layers or as a PCD tip is now irreplaceable as a cutting material. However, what makes it so valuable — its unsurpassed hardness — is often limited by tool geometry.
“With the introduction of powerful laser machines from the LaserSmart series such restrictions are overcome. Using the speed and precision of the Femto Laser, for example, boundaries are literally lifted — both in terms of tool design and quality. The demand for such tools across all industry is rapidly increasing, and these can now be produced not only much better but also considerably faster.”