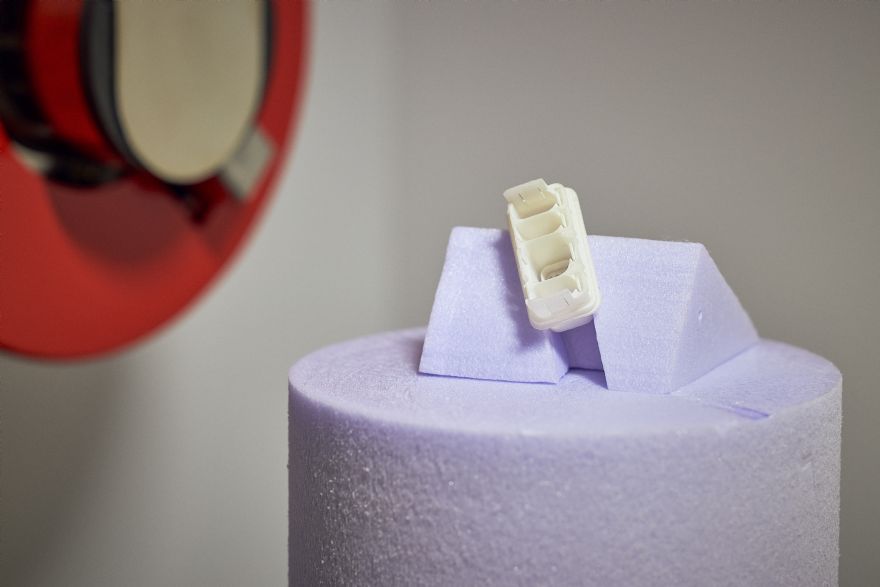
Europe’s largest provider of 3-D printing, injection moulding, and vacuum casting, the Prototal Group has 10 sites throughout Europe. These include:
Prototal UK (formerly 3tamp), which is based in Newbury; and, since 2022, 1zu1 Prototypen GmbH & Co KG. Based in Dornbirn, Austria, 1zu1 has 160 employees, and produces prototypes, small series, and series parts for customers worldwide in a large variety of industries.
Within its manufacturing, 1zu1 uses 3-D printing processes such as laser sintering and stereolithography and says that when developing new components for customers it likes to ‘push the limits’ of what is possible in terms of complexity and precision, adding that metrology plays an extremely important role in measuring and checking ‘the finest details and tightest tolerances relating to both form and position’.
Wolfgang Humml, 1zu1’s managing director, says the company has been using optical measurement solutions for over 10 years and produces several hundred measurement reports per year. “So, we know the limits of optical measurement technology very well; and, against the background that the components we produce were becoming not only increasingly complex but also smaller, it was clear to us that we needed to take the next step in measurement technology — a step that would give better and more accurate results, particularly when comparing 3-D measurement results with 3-D data sets.”
Optical measurement technologyMr Humml identified several criteria as being important in the search for a new measurement solution, particularly as the focus was on the accuracy of the measurement result over the entire 3-D part and not just for the area that can be captured with optical measurement technology. “Here, industrial computed tomography — CT — has clear advantages.
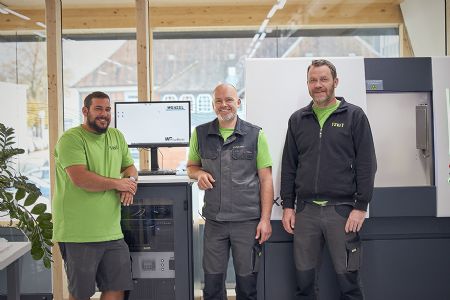
Compared to tactile or optical measuring machines, CT can also measure internal features with high precision in a non-destructive manner; optical metrology clearly has its limits, especially for measuring transparent components — and parts with high-gloss mirror surfaces, as without prior treatment with a laser scanning anti-reflection spray measurement is not possible for such parts. Moreover, the required measurement accuracy cannot be achieved with a spray application.
“Another major advantage of industrial computed tomography is the speed of the scans and evaluation, as thousands of points can be measured within seconds. Moreover, the performance of so-called pallet scans — several components in one scan — offers a shortening of process cycles for even greater efficiency.”
After a comprehensive selection process, 1zu1 chose the ExaCT L CT, a 150kV system from Germany-based
Wenzel which has a subsidiary in the UK Wenzel UK Ltd in Coalville. Mr Humml said: “Critical in our decision was the guaranteed measurement uncertainty of ±5µm, the convincing CT measurement of our five benchmark problem parts, and the impressive surface imaging accuracy without software smoothing. Indeed, we were so impressed with the measurement results that we were happy to order the first machine built with this configuration and are now running the system at our facility. Furthermore, the speed of the scans is such that we were able do about 120 scans in normal working hours in the first three weeks of using it, allowing us to achieve shorter development times — and cost savings for our customers.”
Mr Humml also highlighted the fact that Wenzel’s solution has the smallest footprint in its 150kV class, while offering a scan volume of 400mm in height and 235mm in diameter. “The need for the largest possible measuring volume with a comparatively small machine footprint was another important requirement; and with its small footprint and large scan volume, the ExaCT L offers not only capacity but also ease of transport and installation — without modification of doors or aisles. Furthermore, with an all-up system weight of 2,650kg, this system allows flexibility regarding its location.”
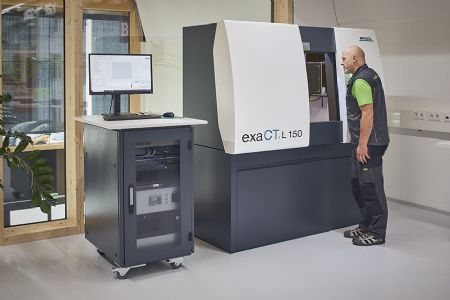
The ExaCT L, which is the latest development in Wenzel’s comprehensive ExaCT series, won Frost & Sullivan’s ‘Global New Product Innovation Award 2020’ — a result that was based on a worldwide market analysis for industrial computed tomography. Mariano Kimbara, a senior industry analyst at Frost & Sullivan, said: “The ExaCT L has optimised X-ray performance combined with a fast detector, allowing it to quickly measure objects and defects. Wenzel has taken an important step into the market with an intuitive user interface that uses intelligent software to automate all measurement parameters and provide robust customer value.
“Moreover, the ExaCT L’s three independent travel axes provide a high level of flexibility, high speeds, short measurement times, and short inspection times, thereby allowing 1zu1 to solve numerous measuring and testing tasks for its customers. These include dimensional evaluations, compensation of shrinkage and warpage, testing for inclusions and impurities, geometric tests, assembly analyses, and process monitoring — with the measurement and test reports always presented in a customer-friendly and comprehensible manner.”
‘Young technologies’Mr Humml went on to say that Industrial computed tomography and additive manufacturing are two comparatively young technologies that can be combined with excellent results. “While additive manufacturing allows new structures to be developed, assessing the quality of these products is an essential requirement, and fortunately this can be readily delivered by CT; and based on the results this gives, correction data is generated — data that can significantly improve both the dimensional accuracy and the mechanical stability of 3D-printed parts. The complex shapes that can be produced by 3-D printing often pose difficulties for conventional measuring systems, but only CT technology can undertake non-destructive material analysis and dimensional accuracy testing.
“Industrial computed tomography provides many advantages. For example, it allows the finest details and the tightest tolerances relating to form and position tolerances to be inspected and measured, with high measurement accuracy over the entire 3-D component — and at high scanning and evaluation speeds, with pallet scans shortening process cycles and increasing efficiency.
“Moreover, internal structures can be captured, as can non-destructive material analysis and dimensional inspection, and a large scan volume can be achieved within a small footprint. Moreover, CT doesn’t suffer the limitations of optical and tactile measuring systems.
“Overall, the Wenzel ExaCT L is a universally applicable testing and measuring device for optimising components and manufacturing processes, as well as shortening development times; and if an analysis or inspection of internal structures is necessary, this can be carried out without destroying the component. Finally, with just one scan, metrological evaluations and analyses can be performed from the generated data.”