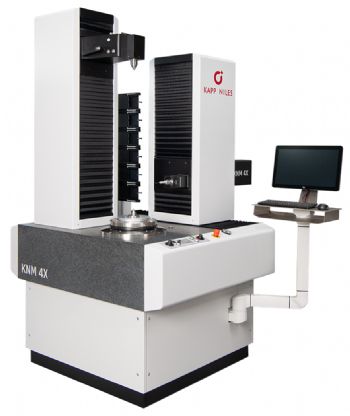
With the electric vehicle (EV) sector ramping up production worldwide, the motors and gearboxes in them place an entirely new set of demands on the manufacturing supply chain. It is here that the
Engineering Technology Group (ETG) comes into its own with its gear grinding technology from
Kapp Niles.
Motors and transmission systems for EVs are not only designed for high speeds and high torques — but they are also very compact. This is not only true for the automotive sector but also for innovative applications such as e-bikes, aerospace applications, drones and much more. These small but high-power and electrically driven gearboxes inspire design engineers to come up with more creative solutions. With the gear manufacturing technology manufactured by Kapp Niles, the Engineering Technology Group (ETG) offers UK manufacturers unique industry-leading innovations for producing electric vehicles and e-bike gearboxes.
As a world leader in gear grinding technology, Kapp Niles is the name trusted by both the automotive and bicycle sectors to successfully implement e-mobility projects. For over 10 years, Kapp Niles has been intensively involved with the topic of gears in e-mobility and has established itself as a pioneer in this rapidly developing industry with customised solutions for the production of gearboxes and gears.
In collaboration with the expertise provided by Kapp Niles, ETG’s team of dedicated experts are always on hand to understand specific e-mobility challenges and they can work closely with customers to deliver world-class results.
The Kapp Niles portfolio is remarkably extensive and encompasses everything from generating/profile grinding machines, profile grinding, topological generating grinding, fine and polish grinding, and also special solutions such as high-speed automated grinding technology, cycloidal gearbox grinding, dressing tools, profile and diamond form rolls and CBN grinding wheels, worms and tools.
Industry 4.0 advancementsThe innovative machines are complemented by metrology solutions that include a complete series of measuring machines, contract measuring services and much more. As an industry leader, this is backed by comprehensive Industry 4.0 advancements that include process, part and condition monitoring, part tracing, remote services and closed-loop digital solutions.
UK manufacturers can investigate some of this technology first-hand with the patented
KX 500 FLEX and the KNM 4X (pictured at top) measuring technology that are available from ETG.
The patented KX 500 FLEX is a gear grinding centre designed for the flexible use of a wide range of tooling and machining technologies. Thus, application-specific production solutions can be configured to perform diverse processing jobs and a wide range of batch sizes efficiently and economically.
Dressable tools for versatile machining processes and non-dressable CBN tools can be used for highly productive manufacturing as well as the grinding of gear geometries with interfering edges. The machine concept is based on a rotary indexing table which incorporates the tailstock and dresser offset against the workpiece spindle. The KX 500 FLEX offers a maximum tip diameter of 500mm, a workpiece length of up to 1m with a maximum helix angle of +/-45 degrees.
Pictured left: specialist Kapp Niles gear grinding technology from ETGComplementing the KX 500 FLEX gear grinding centre is the KNM 4X analytical measuring machine for small to medium-sized workpieces. The KNM series of analytical measuring machines are designed for high-precision measurements of gears, gear tools and rotationally symmetric workpieces.
All guides and base plates are manufactured from granite and are extremely stable in the long term with remarkably low expansion coefficients. Air bearings with emergency operation properties ensure perfect and wear-free guides without short-term errors. Air spring elements underneath the base plates safely shield the machine from jolts and vibrations — all these features combine to deliver unparalleled precision in the measurement of any critical gear components and assemblies.
Furthermore, the KNM series incorporates non-ferrous linear and torque motors on the rotary tables to ensure ultimate positional precision and path accuracy. Despite the compact design, the spacious axis travel ranges ensure a tangential generating motion towards the base circle for any profile.
The KNM 4X offers a maximum workpiece diameter of 450mm with a maximum measurement workpiece length (internal/external) of 400/650mm with a maximum workpiece weight of 500kg. For further details visit
here.