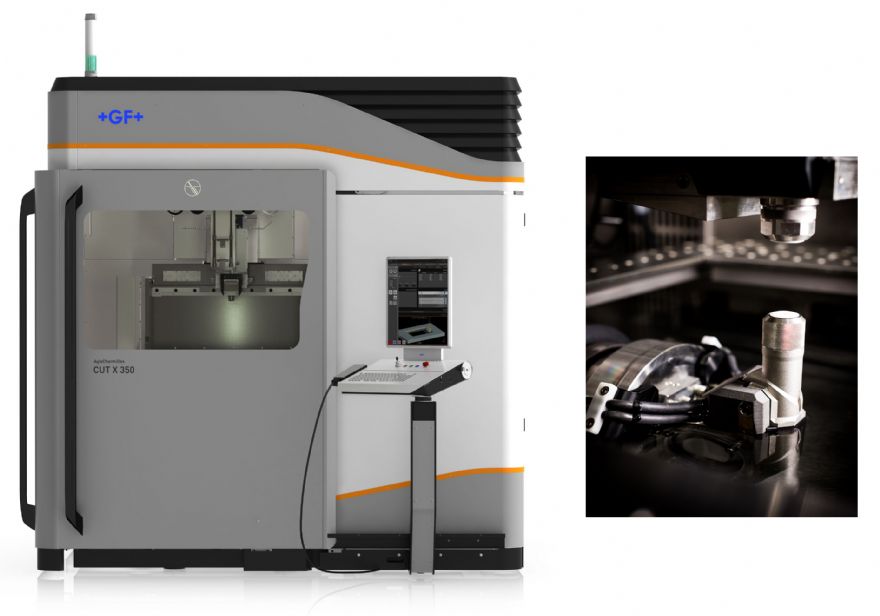
Developed and manufactured by
GF Machining Solutions at its Losone factory in Switzerland, the company’s CUT X series of wire EDM machines are available in two sizes: the CUT X 350 (with a maximum workpiece size of 800 x 550 x 250mm) and the CUT X 500 (with a maximum workpiece size of 1,050 x 700 x 250 mm).
The machines also offer a high level of accuracy, thanks to a new thermal management system and optimised mechanics, which also help improve surface finish quality. Consistent thermal conditions are maintained by the machines’ sealed cabinets and doors, to ensure ‘cold air containment within the workspace as well as controlled air flow’; by keeping heat sources away from the machine’s mechanics, CUT X models perform consistently without the ‘ill effects of temperature fluctuation outside the machine’.
Moreover, the machine’s CNC system collects data from an array of temperature and humidity sensors located inside and outside of the work area ‘to further maintain ambient workspace conditions’. The data drives an artificial intelligence (AI) algorithm that predicts possible thermal deformations, compensates the positioning of the X, Y, U, and V axes accordingly, and ensures high accuracy despite the environmental temperature fluctuations that are common during long cutting cycles.
These machines can also be switched between open and closed wire guides. Open guides are suitable for straight or less than 3deg-taper angle cuts and provide flexibility for varying wire diameters without changing the guide. Closed guides provide high accuracy, speed, and surface finish for taper cuts up to 30deg.
The machines’ ‘Intelligent Power Generators with Direct Power Supplies’ (IPG-DPS) ‘dial in’ the optimum power settings using algorithms based on decades of work by GF Machining Solutions, and thereby deliver specified surface finishes and accuracies at specific speeds. Meanwhile, the machines’ HMI has a 19in vertical touchscreen, along with a full keyboard and mouse; the interface also has a graphics tool for programming both off-line and at the machine — and it is compatible with major CAD/CAM programs.
To prevent wire breakage, the machines use the company’s Spark Track technology and Intelligent Spark Protection System (ISPS) to constantly monitor and evaluate the position of each discharge between the wire and workpiece in real time and against set parameters. Moreover, lights-out productivity is facilitated by an integrated Z-axis touch probe that automatically measures the top surface of the workpiece and aligns the wire perpendicular to this new plane; there are also an automatic slug-management system, automatic wire threading, an integrated wire chopper that reduces downtime, and a double-wire spool with automatic wire changer (AWC) technology.