Three-in-one fast thread solution from Walter
Posted on 30 Apr 2024. Edited by: John Hunter. Read 1006 times.
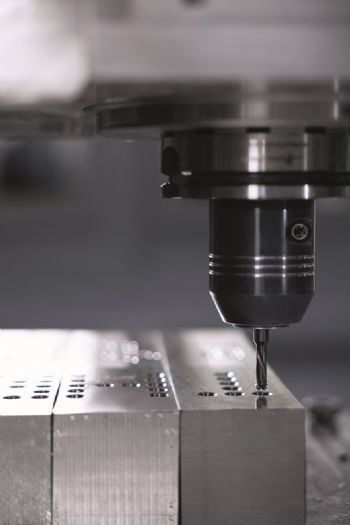
Germany-based
Walter has launched a new range of thread milling tools called ‘Thrill·tec’ which have been designed to combine the machining steps of core-hole drilling and threading in a single tool and operation. This is also true of the TC645 Supreme circular drill/thread mill, which can also produce a chamfer at the thread entry.
Combining work steps improves productivity and makes this three-in-one thread milling cutter ideal for mass production and small series alike. Mass producers can benefit from extended tool life and shorter machining times. Furthermore, the ability to multi-task results in significantly less machine downtime for tool changeovers. The TC645 Supreme pays dividends for small-scale manufacturers because they only have to use one tool, therefore reducing tool changes as well as tool positions in the machine tools.
Furthermore, the left-hand cutting thread milling tool is excellent for multi-tasking operations. This is credited to the milling geometry on its face and the internal coolant supply. It optimises chip removal, even at high cutting speeds and demonstrates a feed per tooth. This means that the tool can be used for blind-hole and through-hole threads in dimensions of 2 or 2.5xD. The universal thread milling cutter excels in all ISO materials from P, M, K, N and S up to 48HRc. This is due in large part to Walter’s WB10TJ grade coating.
In addition to high-process reliability and universal operation, the main advantage of the TC645 Supreme is its cost-effectiveness. Faster machining and reduced indexing times keep the costs per thread relatively low. Walter is offering the TC645 Supreme in dimensions of M4 to M12, UNC8 to UNC½ and G1/16 to G¼ and promises new variants as the line is expanded.