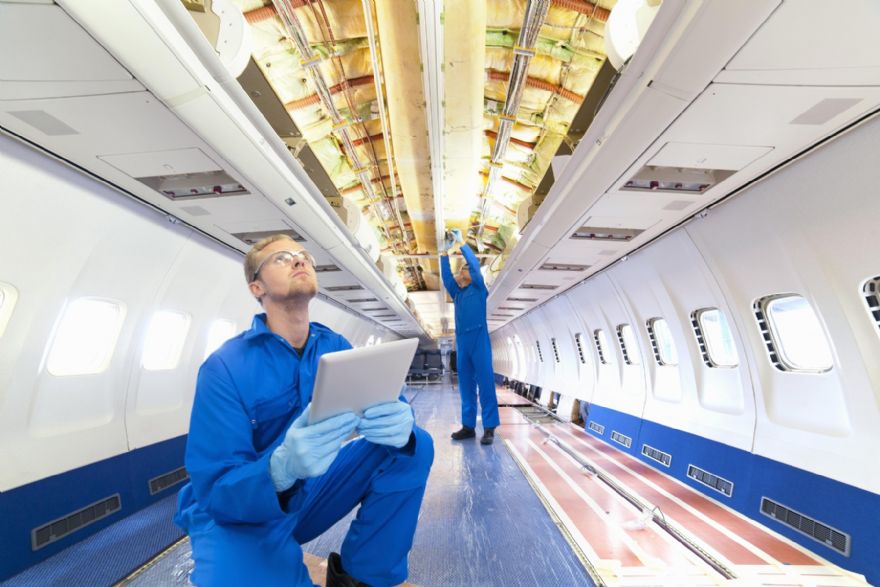
As more airlines look to update their interiors, additive manufacturing (AM) provides a way to rethink part design to simplify or lightweight components. Dave Moore, a 3-D print consultant at
Tri-Tech 3D said: “The main advantage of 3-D printing for aircraft interiors is the ability to customise parts to be lightweight, and to do so quickly. Parts can be designed with complex geometries, thinner walls than their injection moulded counterparts, or consolidated into components that reduce material use and weight — and they can be designed to include fittings or movable features for easy assembly. Moreover, manufacturers can quickly replace damaged interior parts, without the need to stockpile spares.”
Garry Sellick, AM manager at Blackpool-based Airframe Designs Ltd, said: “Plastic cabin parts are typically injection moulded, but this is an expensive approach for a low volume of around 3-4,000 parts per year. Based on initial studies, we believe we can achieve an individual part price reduction with 3-D printing; and with the freedom of AM, we can achieve a weight reduction that can lower carbon emissions.”
Mr Moore continued: “The ability to produce repeatable, accurate 3-D printed end-use parts using aerospace-approved materials is already benefitting many aircraft manufacturers and operators. Indeed, Stratasys aircraft MRO company
SIA Engineering Co, and the 3-D printing bureau
Additive Flight Solutions have produced more than 5,000 parts certified for aircraft cabins. In the functional interior of an aircraft, 3-D printing is being explored for making ducting, vents, plenums, baffles, cable management, electrical housings — and more. AM is also being applied to produce aesthetic parts such as light covers, bezels, trim, signs, door latch components, seat end and arm rest caps.
“Regarding printing technology, the Fortus 900mc from Stratasys has been designed to ensure part repeatability, using such means as controlling moisture; it is also supplied with all the process control documentation needed to certify parts. Alongside dedicated machines, there are numerous materials available with the relevant certifications. These include FST, FAR 25.863 and UL94. Alongside these are materials that offer excellent strength-to-weight ratios, such as ULTEM 9095 and 1010 resins. In many cases, 3-D printing will result in less time on the ground, and reduced inventory spend.”