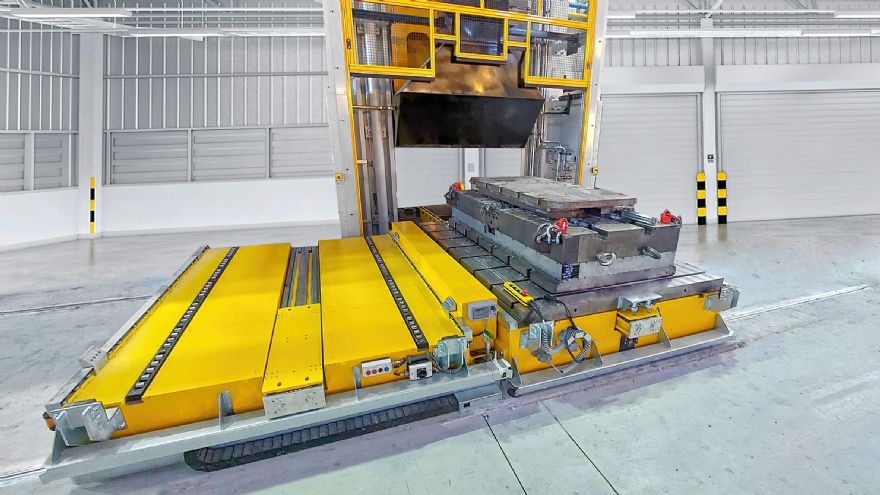
A new, rail-guided changing table for the safe, rapid movement of today's increasingly heavy press tools, moulds and dies within a production plant has been introduced by Germany-based Roemheld. The innovative solution is produced in three versions for loads of up to 15, 25 or 40 tonnes and is available through UK subsidiary
Roemheld (UK) Ltd, Cramlington.
The electrically-driven RWS system is available as a single or tandem cart and comes equipped with two different push-pull arrangements to enable tool exchange on most types of equipment, including vertical forming and injection moulding machines. The changing tables help vehicle manufacturers transport increasingly heavy tools for producing large castings comprising many individual parts, such as when megacasting a vehicle frame or body.
The cart is guided on floor level, round rails having a rolling resistance so low that loads of up to five tonnes can easily be moved manually by one person. The rails are designed to facilitate precise guidance and to prevent dirt ingress and tripping hazards. A safety mechanism ensures that loads can be moved only when the RWS table is firmly attached to either a machine or the storage location.
Consoles that bridge the distance between the machine bed and the die changing cart make tool handling rapid and effortless. The amount of time needed for actual changeover is minimised, as the table is equipped with integrated lifting bars in addition to the pull-push system. It means that the press or moulding machine is able to continue production right up to the moment of tool exchange.
Several presses may be connected by a single table and accuracy of positioning is to within ±0.3 mm. Semi- or fully-automatic die change is possible due to the control system integrated into the cart. Other features include integration with the machine control, the ability to combine with fast-clamping tool systems, low energy consumption and a small footprint on the factory floor.