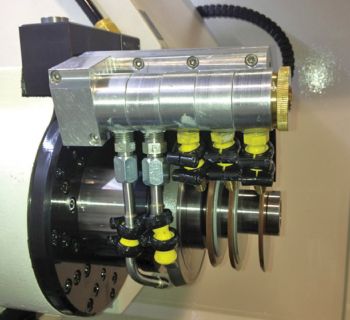
Daventry-based Master Abrasives UK Ltd (
www.master-abrasives.co.uk) is now the exclusive UK and Eire agent for the Grind-Loc range of modular high-pressure reconfigurable coolant supply lines and coherent-jet fluid nozzles from Cool-Grind Technologies.
Master Abrasives’ managing director, Paul Batson, says: “Although the function of the grinding fluid is primarily to cool the component, it also has to cool the grinding wheel, which is very important with resin-bonded diamond wheels. Furthermore, the fluid has to allow the lubricants in it to perform correctly; this is especially important with single-layer super-abrasive wheels.
"The grinding fluid also has to flush the chips from the machine and workpiece area, and clean the wheel — often through the use of high-power jets. This is particularly important when grinding ductile materials using water-based grinding fluids.
“Unfortunately, the application of fluid to a grinding process is a highly neglected area, but if done correctly, it can have a significant influence on the surface finish, surface integrity and productivity achieved. Significant benefits can often be achieved with super-abrasive grinding wheels by improved grinding-fluid application.”
Improvements include: reduced dressing frequency, due to less loading with work material and more-effective use of the EP additives; the use of a harder grade of grinding wheel for improved form holding and reduced dressing frequency; a reduction in thermal damage of the workpiece material, allowing higher removal rates and greater throughput; and a reduction in entrained air (foaming), misting and vapour problems.
Cool-Grind has developed a ‘starter kit’ box-set comprising 49 nozzles, manifolds, a range of pipe fittings and installation tools. The nozzles can be configured to suit any wheel profile; they fit most cylindrical, surface, internal, and creep-feed grinding machines.
There are enough parts in a kit for customers to install the advanced coolant-delivery technology on up to 20 machine tools.
Coherent-jet technology was pioneered at the University of Connecticut’s Centre for Grinding Research and Development in 1992. The project was funded by the USAF, with Pratt and Whitney as the industrial customer. The definition of ‘coherency’ was based on the dispersion of the jet at a distance of 300mm from the nozzle tip.
A very coherent jet is one that doubles in diameter or thickness over that distance. ‘Coherency’ increases the jet’s ability to penetrate the air barrier around the grinding wheel using a concentrated impact energy, and avoids driving additional air into the structure of the wheel.