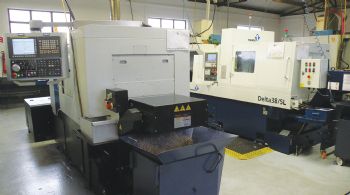
Wexford-based Mann Engineering has been working with the Swiss machine tool builder Tornos (
www.tornos.com) since buying a Deco 2000 sliding-head turning centre over 10 years ago (the Irish sub-contractor has since bought two more Tornos machines).
This machine was bought to replace four cam autos; with its sub-spindle and driven tooling, it cut cycle times from over 2.5min to less than 30sec. It also provided savings in floor space, labour and power consumption.
A decade later, Mann Engineering has seen significant changes to the manufacturing landscape in Ireland, with customers no longer ordering large batches. Company director Rolf Fuhrmann says: “Our regular batch sizes have fallen from 5,000-30,000-off to anything from 200 to 5,000, so we needed to review our machining capabilities.
"Nothing could match the Deco for its productivity, precision and quality levels, but the set-up times prevented it from being a viable option for small batches in the region of 200. We just couldn’t compete on cost when set-up times were taken into account.”
Mann needed the combination of flexibility and productivity for parts below 38mm in diameter (the company’s four triple-turret twin-spindle Japanese turning centres accommodate the turning of parts up to 64mm in diameter).
It decided to buy a Tornos ST26 (installed in August 2014) and a Delta 38 turning centre (installed in September 2014) to replace the ageing Deco machine, increase capacity and relieve some of the workload on the larger twin-spindle machines.
As soon as the Delta 38 and ST26 were up and running, Mann was able to cut set-up times by over 70%, making it competitive on smaller batch runs. “We will do a job change-over every day on each machine and sometimes twice a day, with a longer-running batch being loaded in the evening for ‘lights out’ machining. The new Tornos machines have made us competitive, and their productivity is excellent.”
Contributing to their productivity are the integrated spindle motors and pneumatically activated clamping mechanisms, which significantly cut the time required for workpiece clamping and bar feeding compared with hydraulic systems. Additionally, the kinematics of the Delta 38 and ST26 — plus their modular tooling arrangements — have also contributed to flexibility and cycle time savings.
“Compared to hydraulic chucks and collets, the Tornos system has cut the time to feed a workpiece, clamp and unclamp it by 5sec per part. In addition, the tool configuration sees every tool no more than 50-60mm from the workpiece at all times; our turret machines have to move tools by up to 350mm before cutting can commence.
"As a result, a typical cycle time of 40sec has been cut to just 20sec on the Delta 38. We now have a 38mm-diameter machine that is relieving the workload of our larger machines, while the ST26 is remarkably productive and flexible — and capable of producing all our parts below 26mm in diameter.”