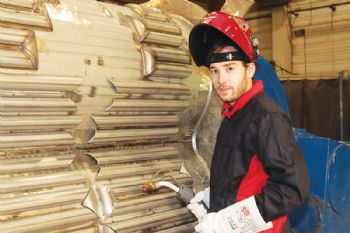
Agitator vessels are used wherever something needs to be stirred on an industrial scale, as in the chemical, pharmaceutical and food industries.
AST Apparatebau GmbH — based in Wilnsdorf, Germany — is a manufacturer of this type of equipment.
The media in agitator vessels are not just stirred, they can also be heated or cooled.
In wax production, for example, different waxes are further processed at different temperatures, while in some pharmaceutical applications, jackets even cool the contents of the agitator vessels down to -80°C.
Heating or cooling in agitator vessels is carried out by means of a half-pipe coil that is usually welded onto the vessel wall in what could be described as a spiral formation; these half-pipes are pipes cut longitudinally, with the surface of the vessel effectively forming the bottom of the pipe (the cooling or heating liquid flows inside this pipe).
The diameters of agitator vessels range from 800mm to 2.5m, and the length of the weld seams required to produce a finished vessel can range from almost 10m to several hundred metres in total.
The demands on these weld seams are significant, and they have to comply with industrial standards that define specific weld preparations for the half-pipes (as well as different versions of half-pipe).
Root pass welding is conducted in a protective gas atmosphere; an endoscope is then used to determine whether the requirements of the standards have been met.
Typically, the joining processes for seams are TIG welding for the root pass and MAG welding for the cover pass. The estimated welding time for 1m of TIG weld seam for the root pass is 20-25min.
Increasing productivity
Following consultation with Rudolf Federrath from the welding machine manufacturer EWM AG (
www.ewm-group.com) — based in Mündersbach, Germany, and with a UK sales and service centre in Morpeth, Northumberland (e-mail: ) — there followed the installation of a tigSpeed wire feeder, which resulted in AST seeing a significant increase in productivity.
This unit, which has been specially designed and constructed for TIG welding, allows both cold-wire feeding and working with hot wire (with the filler wire pre-heated, the deposition rate can be increased by up to 60% compared to manual TIG welding).
Mr Federrath says: “What makes tigSpeed special is that not only is the wire continuously fed, as with MIG/MAG welding, but an additional forward and backward movement is superimposed.

“In this way, the wire feeder mimics the manual welding process in TIG welding, whereby the welder repeatedly pulls the filler wire out of the arc.
“The increase in productivity from using tigSpeed is enormous. The average welding time for 1m of weld seam is reduced from 20-25min down to just 5-6min.
“In the case of continuous weld seams, this means a saving of up to 75% for the root pass when compared to conventional TIG welding with manual feeding of the filler wire.”
EWM says that this greater efficiency is due to both the higher deposition rate of the hot wire and the ease of operation offered by tigSpeed.
Mr Federrath said: “Since the filler wire comes off a roll, there is no need to constantly interrupt the welding process to change the consumable — and the welding torch is very easy to work with.”
In addition to standard TIG cold/hot wire torches, EWM also offers a version with a TIG torch integrated into a MAG grip.
This is the version chosen by AST, which is now benefitting from TIG welding that feels like MAG welding — plus greater welding speed, thanks to the forward and backward movement superimposed on continuous wire feeding.
Moreover, the welder can control the weld pool in exactly the same way as when welding with the manual feeding of the wire — without needing to worry about feeding.
Special plant
AST’s particular strength is the manufacture of special plant, so its agitator vessels may deviate from the usual round shape and spiral winding of the half-pipes.
One example of this is where the vessel is almost completely covered with cooling coils. For this purpose, the half-pipes are mitred and welded together at the corners.

This minimises the distance between the cooling coils, resulting in the greatest possible heat exchange between the medium and the vessel.
For this particular application, the total length of the weld seam can be as much as 112m, with TIG hot-wire welding used on the long straight lines, while conventional TIG welding (with manual feeding of the filler wire) is used for the corners.
As a result, the total length of the weld seam is equally divided between the two processes; and while only half of the weld seam length is welded with hot wire, the welding time is reduced by up to 40% compared to TIG welding with manual feeding of the filler wire.
Joachim Jung, technical manager at AST, said: “What’s particularly attractive about TIG welding with tigSpeed is the possibility of further automating the welding task.
“Currently, this is not an option for us, as the welder has to compensate for any gaps that may occur when the half-pipes are tack-welded onto the vessel wall. An automated system can’t do this.
“That said, our next step will be to install a nozzle-welding system based on TIG hot wire.
“There are a large number of nozzles on every agitator vessel that need to be welded, and TIG hot-wire welding can be used to its full potential here as well.”