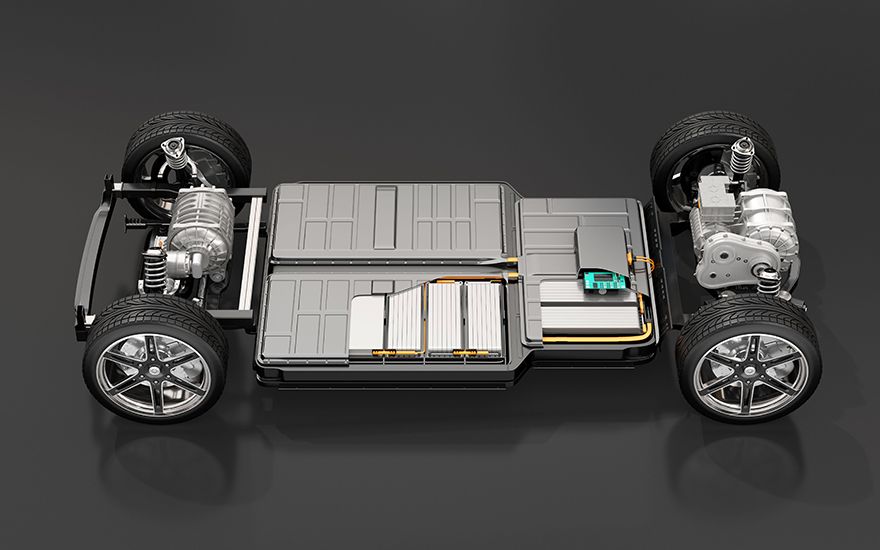
Automotive original equipment manufacturers (OEMs) are getting more involved in battery cell production, which is moving physically closer to vehicle assembly plants.
McKinsey & Company reports that battery technology, durability, and performance will be key differentiators that set OEMs apart.
Fernando Oliveira, global manager for automotive aluminium at metal cutting specialist
Sandvik Coromant, explains how its new concept
M5F90 face-milling cutter could be crucial for helping OEMs get ahead of their peers.
Battery systems will continue to evolve over the coming years and new developments and shapes will be required. For OEMs, this will entail producing near-net shaped battery system parts based on more complex designs. Machining these designs will require efficient and lighter-cutting tools, to minimise impact on the machine tool and ensure the component stays in shape.
The role of OEMs is also evolving as they get more involved in battery production, which McKinsey & Company attributes to ‘the backward integration of OEMs from packs and modules up to cell production.’ At the same time, the race is on to build lighter and more efficient electric vehicles (EVs) that travel for longer distances with a maximised vehicle range per charge.
Furthermore, manufacturers must produce these more-complex components to the highest quality and with high productivity. How can manufacturers achieve this while maintaining a low cost-per-component? The answer lies in more efficient cutting tools, which have good accessibility and are as light as possible to allow quick tool changes. Manufacturers are turning to ‘lightweighting’, which entails building cars and trucks that are less heavy as a way to achieve better fuel efficiency and handling.
Reduce CO2 emissions Another McKinsey & Company study,
Lightweight, heavy impact, calculates that ‘Lightweight measures can help reduce CO
2 emissions to a certain extent (approximately 0.08g CO
2 reduction per kilogram saved).’ It concludes that ‘If an OEM manages to reduce the vehicle weight by 100kg, it saves approximately 8.5g CO
2 per 100km.’
As one of the lightest metals in the world, aluminium is established lightweighting solution. Aluminium is almost three-times lighter than iron and, although of lower strength than iron, is still very strong and corrosion resistant. From a design engineering perspective, it has been found that placing conventional cast iron parts with aluminium alloys can reduce the overall weight of the engine block by up to 40–55%.
A further advantage of aluminium is that it is very recyclable and can be melted and reused without any harm or change to its mechanical properties. In fact, approximately 75% of all aluminium ever produced is still in use today, which is testament to the material’s usefulness in OEMs’ sustainability strategies.
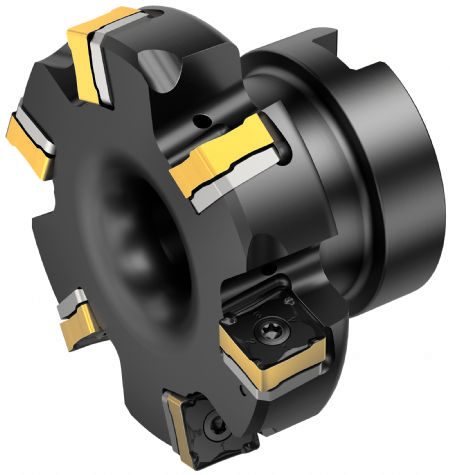
The power train of a European passenger car typically contains around 80kg of aluminium, which means these parts: the engine, gear box, suspension parts and housings are an obvious area of interest for light weighting measures. Aluminium may also be used in the batteries themselves: the
EU-China Energy Cooperation Platform (ECECP) recommends aluminium-air (AI-air) batteries as an ‘inexpensive, light and powerful’ alternative to lithium-ion (Li-ion) batteries.
Aluminium battery racks generally have smaller faces with more threads, holes and other features. Another important consideration is electric battery racks for trucks, specifically larger models driven away from built-up areas, which measure up-to two metres in length.
Battery racks require an assortment of machine tools and applications like milling, rimming and more. Yet even larger battery racks do not require large tools and are, instead, made up of smaller faces with more features, threads, and holes. Therefore, they require shoulder and face milling tools or reamers that can produce components to the required quality and tolerances.
For machining battery racks, Sandvik Coromant recommends using its M5 family of dedicated automotive aluminium milling cutters, including the M5F90 face-milling cutter designed to machine parts without burring, scratching or chipping. The cutter is dedicated to machining thin-wall aluminium parts and, to achieve this, it is equipped with a smaller cutter body of 25-80mm in dia. The M5F90 also contains brazed Polycrystalline Diamond (PCD) tips, so requires no adjustment and secures very reduced runouts. This enables high feed rates while also eliminating cutting vibrations.
An ideal applicationIn one instance, the M5F90 was used to machine an aluminium battery tray. This was an ideal application for the new concept face-milling cutter because the application required that the tool be used to clean surfaces in the first machining stage of the newly-cast aluminium part in a single operation, without burring.
Its dimensions were approximately 980 x 600 x 130mm. Overall, 48 tools were used to machine the component including solid carbide drills, solid carbide end mills, high-speed steel (HSS) taps, brazed PCD reamers, brazed PCD milling cutters and, lastly, the M5F90 cutter. The aluminium component was machined in a five-axis machining centre, equipped with a HSK 63 high-speed tool holder.
The M5F90’s brazed PCD inserts have stepwise cutting edges in both senses, radially and tangentially. This characteristic lowers the power consumption allowing to run with higher cutting parameters, which eliminates burrs and reduces vibrations during machining. The latter advantage, in particular, helps give reliable performance with improved tool life and increases the number of components machined.
In the end, the battery tray machining application demonstrated a key advantage of the M5F90. Specifically, that it enables roughing and finishing in a single operation, thus saving time. This was demonstrated within the machining of the aluminium battery tray; the component was machined in 20.3min. With this enhanced tool performance, OEMs can get more involved in producing battery systems, while setting themselves apart from competitors.