Pictured are Jon (left) and David Littlechild. All photos: Still Vision PhotographyCambridgeshire-based
Shearline Precision Engineering Ltd, established in 1973, with little more than £60 by its founder David Littlechild, in his parents’ summerhouse in Cambridge, is an impressive British manufacturing success story, continually evolving over the years into the multi-million-pound business it is today. The company offers a complete manufacturing solution, from prototyping and pre-production to full serial production. The company prides itself as being among a very few companies in the UK that can provide such a diverse range of services.
Shearline, which still remains a family-run engineering business, is now based in a purpose-built factory in Ely, Cambridgeshire, in the middle of the ‘Cambridge Phenomenon’ and the parts it manufactures can be found in many products around the world and even in outer space — the company manufactured the cases for two Raspberry Pis that were sent to the International Space Station.
Kicking of the 50th anniversary celebrations last week at an event attended by
Machinery Market, Make UK’s regional director Charlotte Horobin said: “Reflecting on the past 10 years alone, we have seen five Prime Ministers, a Scottish referendum, an EU referendum, a global pandemic and many other geopolitical shocks. So congratulations to the team for not only navigating through the last 10 years but for doing so for half a century.”
Breadth of serviceShearline’s current managing director Jon Littlechild, David’s nephew, said: “Shearline has 170 customers and manufactures over 2,700 different component numbers — last year we made almost one million parts. There are very few UK companies that can offer the breadth of service that Shearline does, including design for manufacture, CNC, fabrication, welding, laser marking, powder coating, assembly, kitting and stockholding.”
The company describes itself as ‘the power behind a good many thrones’ and its components can be found in a wide variety of products including inkjet printers, innovative medical devices and beauty advancements, F1 motor racing and globally renowned car marques, electric vehicles, electronics, defence, aerospace and components for the nuclear industry.
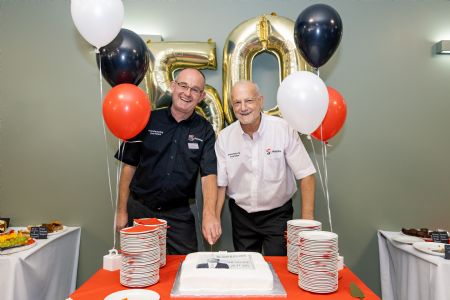
He said that the biggest single factor in the success of the company was a contract with instrumentation giant LKB Biochrom which has remained a loyal customer for more than 45 years. Another catalyst for expansion was the development of the inkjet printing sector, principally through Domino, Linx and Willett (now Videojet) — all of which are still customers today. Over the years, Shearline has continually invested in the latest machinery which, in turn, has boosted capability and enabled the sub-contractor to take on increasingly large and complex jobs.
David said: “Investing in new machines and the latest technology has always been a priority for Shearline and has allowed us to maintain efficiency, quality — both crucially important when competing in competitive global markets. The investment strategy has included one of the largest five-axis machining centres operating in a sub-contract environment in the UK at our subsidiary Shear XL which is just down the road.”
The company continues to expand into a variety of new markets such as robotics, wind turbines, electric vehicle technology, and medical and electron microscopes and has had AS9100 accreditation for the past 10 years which enables it to supply parts to the aerospace and defence industries.
Acquisitions have also played a significant part in the success of Shearline. In 2007, the company acquired
HLT which enabled it to machine, scribe and cut ceramics materials, and in 2010 it bought the assets of
Shear XL (SXL), a motorsports company which specialises in the machining of castings, predominantly for the motorsports and automotive industries, supplying into some of the leading transmission companies in Europe. It also supplies customers in the agricultural, oil and gas, defence, nuclear and 3-D printing sectors.
More and more demand for magnesiumSpencer Curtis, SXL’s manager, said: “On the whole we machine two types of material at this site, aluminium and magnesium, although we do process cast iron occasionally. Significantly, we are seeing more and more demand for magnesium particularly from our motorsports customers as the material’s density is only 66% than that of aluminium, meaning significant weight savings and all important time savings for racing.
“It is also becoming much more widely used in in the aerospace sector where weight savings have huge financial benefits with the reduction in the amount of fuel required. Machining magnesium does come with additional risks though, the main one being that once turned into powder or ‘chips’ it becomes extremely flammable.
“This is one of the main reasons we do not cut this material dry — keeping it cool with temperature-controlled coolant significantly reduces the fire risk as well as preventing any of the magnesium dust from becoming airborne which can also have health and safety implications for the staff. We put a lot of work into finding a coolant that was suitable for both magnesium and aluminium so we don’t need to do full machine clean downs when swapping between the two materials. This means minimal machine downtime allowing us to keep the spindles cutting metal and maximising output.”
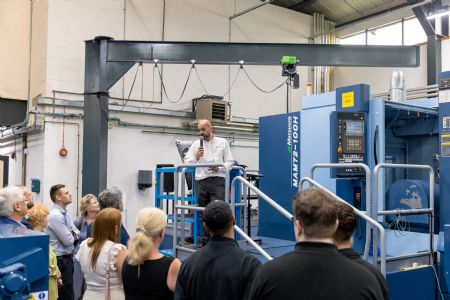
The feather in SXL’s cap is a Matsuura MAM-100H, the largest five-axis mill that Matsuura manufactures which gives the company a cutting envelope of around 1m
3 depending on depth and angles of drilling required and it is capable of holding 240 tools.
Spencer added: “With designs seemingly getting larger and more complex it was important we also increased our five-axis capability to keep up with our customers ever growing demands. We consider this machine a bit of a coup for Shear XL as the £1 million outlay required to purchase one of these usually means only automotive manufacturers like Mercedes and Cosworth have these machines in their workshop. It allows us to manufacture very large castings that we may have previously had to decline.”
David — who these days acts in a consultancy capacity — and managing director Jon, say one of the biggest challenges over the years has been finding and retaining suitably skilled staff. To address this issue Shearline has developed its own apprenticeship scheme which produces high-quality engineers following a four-year training programme.
Longstanding members of staffJon said: “The company has some very longstanding members of staff, and is nothing without its people. After David, who has been here for 50 years, we have one member of staff of 34 years, and 10 more people with over 25 years’ service. I started on a one-year contract and am still here after 27 years! Many of our former apprentices are still here to. One of them is running the fabrication department and others have been at Shearline for more than 24 years.”
Similarly, being aware of the gender disparity in the engineering sector and how important it is to make sure women are fully represented, Shearline always ensures that equality is top of the agenda when selecting its annual apprentice intake — two of the current apprentice cohort are female. In terms of the workforce overall, almost a third of the company’s entire staff are women, several of them talented engineers, while a good number are managers, right up to the finance director.
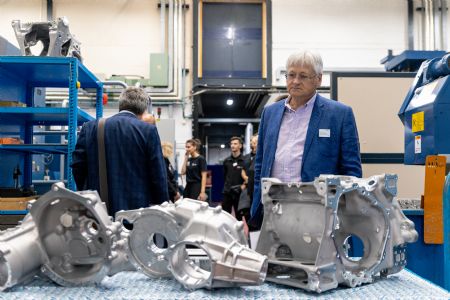
Ever mindful of the macro-economic situation, Shearline senses a further opportunity for growth, as David said: “One of the reasons I believe the future for Shearline is so good is that the recent supply chain problems with China has forced companies to consider reshoring their manufacturing operations.”
He continued: “Challenges for the future include fluctuating energy prices, which in turn influence many other commodities that Shearline purchases such as materials. To partially mitigate this, we have installed over 0.5MW of solar panels which will account for around 25% of our energy usage. Shearline has for many years invested in ‘green’ manufacturing long before environmental consideration was at the forefront of peoples’ minds — for example, recycling materials, installing a combined heat and power unit, and coolant management systems that reduce oily waste by as much as 75%. My aim is to leave the world in a better place than how I found it and Shearline is trying exceptionally hard to make this happen.”
Jon concluded: Shearline has always been a company that has been able to adapt to problems and opportunities and I would like to think that the management structure here allows us to be agile, enabling rapid change when required. If opportunities arise from existing or future customers then we will rise to the challenge and will invest in the people, the plant and the space to achieve any goal. We have plenty of available space to expand around the factory and we are also always looking at new equipment to expand our portfolio and provide us with the ability to take on new work.”