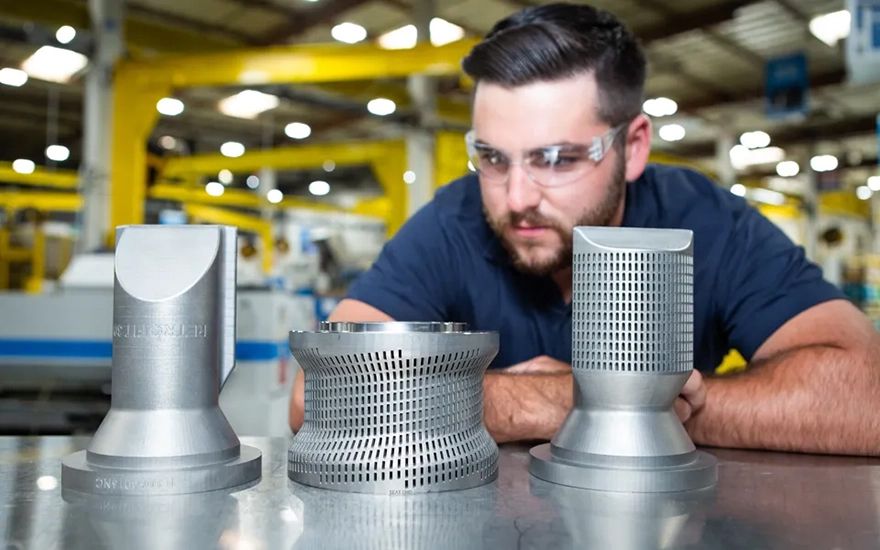
West Sussex-based
Ricardo plc , a global strategic environmental and engineering consulting company, has undertaken an in-depth life-cycle assessment of aftermarket valve components, which has concluded that additive manufacturing (AM) has a significantly lower impact on the environment.
Commissioned by
IMI Critical Engineering (IMI) for its AM technology Retrofit3D, the study identified opportunities to reduce the climate change impact of certain replacement valve parts. As part of this process, the valves’ global warming potential can now be reduced by between 85%-96% depending on valve size and repair scenario.
IMI designs and manufactures highly specialised valves and actuators to help control the flow of steam, gas and liquids serving the oil and gas, petrochemicals, water and power industries. The valves used in these sectors are subject to harsh operating conditions, which can lead to erosion or cavitation. When this type of damage is found, upgrades are required in the form of a new disk stack.
Life-cycle assessmentsRicardo was asked by IMI to apply its expertise in life-cycle assessments to determine the environmental impact of three replacement scenarios for two different valve sizes (large and small). These scenarios included: replacement of disk stack using only traditional manufacturing methods; replacement of the full valve using traditional manufacturing methods; and replacement of the disk stack only using AM.
The life-cycle assessment found that the AM disk stack replacement manufactured by Retrofit3D was the preferable choice across all the environmental indicators analysed. The small valve resulted in 146kg of CO
2 equivalent when the Retrofit3D AM process was used to produce the replacement disk stack. The large valve resulted in 1,360kg of CO
2 equivalent using the same process.
All calculations were based on an assumed system lifetime of 10 years. For the large valve, this represented a 96% climate change impact saving when compared with replacement of the full valve via traditional manufacturing, and a 94% saving when compared with replacement of the disk stack only via traditional manufacturing. For the small valve, it represented a saving of 87% and 85% respectively. Any use efficiency savings were not accounted for in this study due to the wide range of potential-use scenarios. If these were accounted for, the savings may be higher.
Analysis of the downstream transportation methods for the new valve and components showed that transitioning from air freight to 80% sea freight and 20% road freight would reduce the total climate change impact in all replacement scenarios by 97%.
Environmental impactSam Hinton, head of life cycle assessment at Ricardo, said: “Corporations are increasingly challenged to take active steps to minimise their environmental impact and communicate this in a robust manner, free from ‘green washing’ claims. Ricardo has provided IMI Critical Engineering with a thorough life-cycle assessment that has been critically reviewed and considers 16 environmental indicators.
“It identifies that the Retrofit3D solution has the lowest impact of all the scenarios assessed for all 16 indicators. In short, it can achieve the greatest decarbonisation potential, without shifting burdens to other environmental issues. IMI can now communicate the reduced environmental impacts associated with its solution confident in the knowledge that this is backed up by a thorough life-cycle assessment of the comparative solutions.”
Bertrand Maillon, Retrofit3D business leader at IMI, added: “3-D printing is a ‘game-changing’ method for valve manufacturing. Improving reliability and performance while offering, in Retrofit3D, a less materially intensive solution is essential for us and our customers. This technology is a disruptor for maintenance, repair and operations and spare parts supply, and promises a great future for innovative flow control solutions.”
This life-cycle assessment for IMI is the latest example of Ricardo applying its deep scientific analysis and significant experience at the forefront of product sustainability to enable clients to develop more sustainable products or demonstrate their advanced environmental credentials. Ricardo is currently working with the manufacturers around the world to quantify and reduce the environmental impacts of their products.
Download a free copy of the report
here.